Method and device for determining joint rotation angles of serial robot
A technology of rotation angle and robot, applied in the field of robot, can solve the problem that the model cannot satisfy continuity, minimum and integrity at the same time
- Summary
- Abstract
- Description
- Claims
- Application Information
AI Technical Summary
Problems solved by technology
Method used
Image
Examples
Embodiment Construction
[0082] In order to make the object, technical solution and advantages of the present invention clearer, the present invention will be described in further detail below in conjunction with specific embodiments and with reference to the accompanying drawings.
[0083] The robot adopts a series open-chain structure, that is, the connecting rods of the robot are connected in series by rotating joints or moving joints. One end of the connecting rod is installed on a fixed support (base), and the other end is in a free state, and various tools can be installed to realize robot operations. The function of the joint is to make the two connecting rods connected to each other move relative to each other. The transmission of the joint adopts a modular structure, which is realized by the cooperation of various transmission structures such as bevel gears, synchronous toothed belts and harmonic reducers. The joints of the robot are driven by servo motors and stepping motors, and the robot ...
PUM
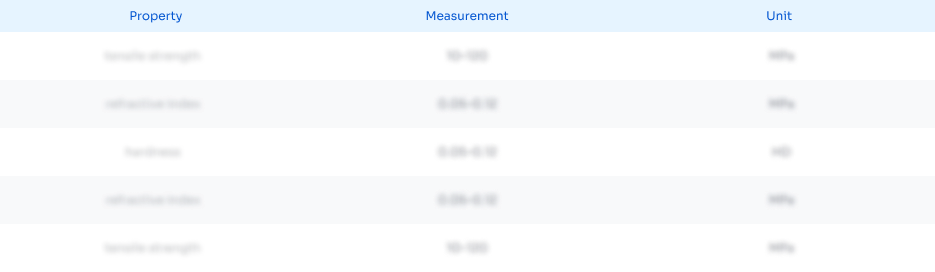
Abstract
Description
Claims
Application Information

- R&D
- Intellectual Property
- Life Sciences
- Materials
- Tech Scout
- Unparalleled Data Quality
- Higher Quality Content
- 60% Fewer Hallucinations
Browse by: Latest US Patents, China's latest patents, Technical Efficacy Thesaurus, Application Domain, Technology Topic, Popular Technical Reports.
© 2025 PatSnap. All rights reserved.Legal|Privacy policy|Modern Slavery Act Transparency Statement|Sitemap|About US| Contact US: help@patsnap.com