Unmanned engineering detection vehicle
An engineering inspection and unmanned driving technology, which is applied to bridge parts, bridges, buildings, etc., can solve problems such as poor control of movement, impact on detection accuracy, and large inspection vehicles
- Summary
- Abstract
- Description
- Claims
- Application Information
AI Technical Summary
Problems solved by technology
Method used
Image
Examples
Embodiment Construction
[0034] In order to further explain the technical means and effects adopted by the present invention to achieve the intended invention purpose, the specific implementation, features and effects of the unmanned engineering inspection vehicle proposed according to the present invention are described in detail below.
[0035] Such as figure 1 As shown, the present invention discloses an unmanned engineering inspection vehicle, comprising:
[0036] The moving device includes two groups of pulley assemblies symmetrically arranged on the I-beam 91 on both sides of the bottom of the bridge 9 to be detected and used to provide the pulley assembly with a power device that moves back and forth along the I-beam 91, wherein the power device is a motor , the movement of the pulley assembly on the I-beam 91 at the bottom of the bridge 9 is driven by the motor;
[0037] The vertical direction track 4, the two ends of the vertical direction track 4 are respectively connected with two groups o...
PUM
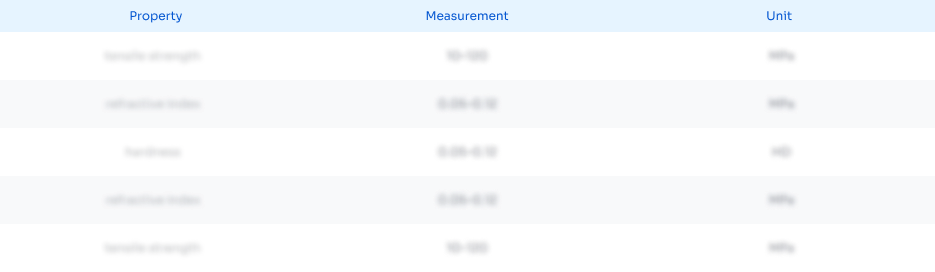
Abstract
Description
Claims
Application Information

- Generate Ideas
- Intellectual Property
- Life Sciences
- Materials
- Tech Scout
- Unparalleled Data Quality
- Higher Quality Content
- 60% Fewer Hallucinations
Browse by: Latest US Patents, China's latest patents, Technical Efficacy Thesaurus, Application Domain, Technology Topic, Popular Technical Reports.
© 2025 PatSnap. All rights reserved.Legal|Privacy policy|Modern Slavery Act Transparency Statement|Sitemap|About US| Contact US: help@patsnap.com