Multi-axis mechanical arm with electric clamping claw
A technology of manipulators and grippers, applied in the field of multi-axis manipulators, which can solve problems such as changes in motion coordinates, unfavorable repetitive positioning of robots, and impacts
- Summary
- Abstract
- Description
- Claims
- Application Information
AI Technical Summary
Problems solved by technology
Method used
Image
Examples
Embodiment Construction
[0066] The following will clearly and completely describe the technical solutions in the embodiments of the present invention with reference to the accompanying drawings in the embodiments of the present invention. Obviously, the described embodiments are only some, not all, embodiments of the present invention. Based on the embodiments of the present invention, all other embodiments obtained by persons of ordinary skill in the art without creative efforts fall within the protection scope of the present invention.
[0067] figure 1 It shows a schematic diagram of the three-dimensional structure of the multi-axis mechanical arm with electric grippers according to the embodiment of the present invention, figure 2 shows the front view of the multi-axis robotic arm with electric gripper according to the embodiment of the present invention, Figure 5 It shows the top view of the multi-axis mechanical arm of the electric gripper of the embodiment of the present invention. In order...
PUM
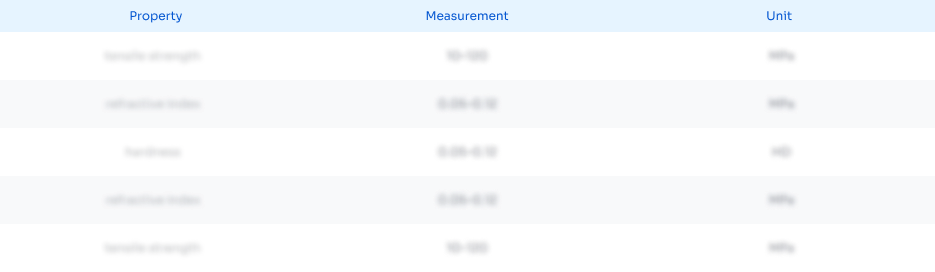
Abstract
Description
Claims
Application Information

- R&D Engineer
- R&D Manager
- IP Professional
- Industry Leading Data Capabilities
- Powerful AI technology
- Patent DNA Extraction
Browse by: Latest US Patents, China's latest patents, Technical Efficacy Thesaurus, Application Domain, Technology Topic, Popular Technical Reports.
© 2024 PatSnap. All rights reserved.Legal|Privacy policy|Modern Slavery Act Transparency Statement|Sitemap|About US| Contact US: help@patsnap.com