A multi-finger robot end effector with variable grasping range and method
A technology of end effector and robot, applied in the direction of manipulator, manufacturing tool, chuck, etc., can solve the problem of different replacement, achieve smooth and smooth motion, and solve the effect of low efficiency
- Summary
- Abstract
- Description
- Claims
- Application Information
AI Technical Summary
Problems solved by technology
Method used
Image
Examples
Embodiment Construction
[0033] Aiming at the deficiencies of the prior art, the present invention proposes a multi-finger robot end effector with a variable grasping range and a method. By using two motors to drive the main shafts that move independently, one is used to drive the end effector to lift The other one is used to drive the end effector to perform opening and closing movement. The two movements are carried out independently, which can realize the movement with variable grasping diameter and grasping height. In addition, in the present invention, a plurality of evenly distributed circular motion guide grooves are provided to make the equally uniformly arranged fingers move synchronously, avoiding the phenomenon of movement stagnation, and the present invention will be described in detail below with reference to the accompanying drawings.
[0034] like figure 1 Shown is a structure diagram of a multi-fingered robot end effector with variable grasping range. figure 2 Shown is a view of the ...
PUM
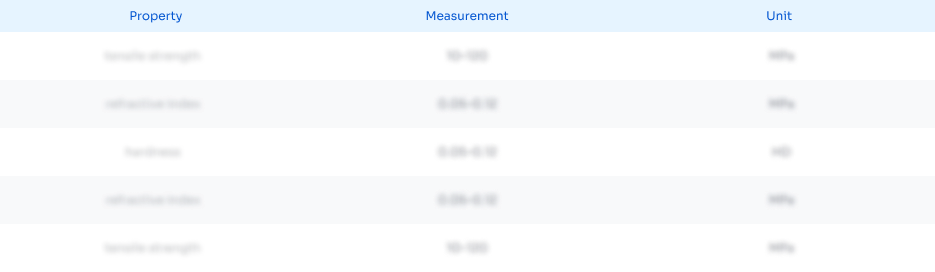
Abstract
Description
Claims
Application Information

- R&D Engineer
- R&D Manager
- IP Professional
- Industry Leading Data Capabilities
- Powerful AI technology
- Patent DNA Extraction
Browse by: Latest US Patents, China's latest patents, Technical Efficacy Thesaurus, Application Domain, Technology Topic, Popular Technical Reports.
© 2024 PatSnap. All rights reserved.Legal|Privacy policy|Modern Slavery Act Transparency Statement|Sitemap|About US| Contact US: help@patsnap.com