Six-shaft robot control system used for pipe fitting welding
A six-axis robot and control system technology, applied in welding equipment, auxiliary welding equipment, program control manipulator, etc., can solve the problems of inaccurate center point of welding torch, inconvenient operation, low opening degree, etc., to improve efficiency and welding quality , Improve the efficiency of welding and reduce the effect of movement time
- Summary
- Abstract
- Description
- Claims
- Application Information
AI Technical Summary
Problems solved by technology
Method used
Image
Examples
Embodiment Construction
[0029] A six-axis robot control system for pipe welding, including a main control board, an embedded controller and a motion controller, the motion controller is integrated in the embedded controller, and the motion controller is connected to the six joint axes through the bus The motor servo driver is further connected to the motor, the main control board is connected to the embedded controller through the bus, and the motor linkage of the six joint axes is controlled by the embedded controller and the motion controller to control the motion posture of the robot;
[0030] The main control board includes a logic control module, a path planning module, a motion control module and a network control module;
[0031] The logic control module is used to optimize the program and complete the logic control operation;
[0032] The path planning module is used to solve the motion trajectory of the end, select the appropriate motion trajectory according to the size of the welding workpi...
PUM
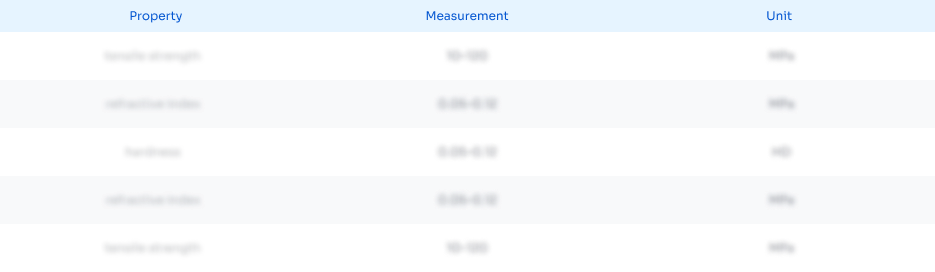
Abstract
Description
Claims
Application Information

- R&D Engineer
- R&D Manager
- IP Professional
- Industry Leading Data Capabilities
- Powerful AI technology
- Patent DNA Extraction
Browse by: Latest US Patents, China's latest patents, Technical Efficacy Thesaurus, Application Domain, Technology Topic, Popular Technical Reports.
© 2024 PatSnap. All rights reserved.Legal|Privacy policy|Modern Slavery Act Transparency Statement|Sitemap|About US| Contact US: help@patsnap.com