Weld tracking application adaptive fuzzy control method
A technology of adaptive fuzzy and control methods, applied in the direction of adaptive control, general control system, control/regulation system, etc., can solve the problems of rough control process, unknown robot mathematical model, and inability to send directly, and achieve the goal of solving the problems in the control process. Effect of Stable, Real-time Accurate Adaptive Fuzzy Control
- Summary
- Abstract
- Description
- Claims
- Application Information
AI Technical Summary
Problems solved by technology
Method used
Image
Examples
Embodiment Construction
[0058] The purpose of the invention of the present invention will be described in further detail below in conjunction with the accompanying drawings and specific embodiments, and the embodiments cannot be repeated here one by one, but the implementation of the present invention is not therefore limited to the following embodiments.
[0059] A kind of self-adaptive fuzzy control method of seam tracking application, comprises steps:
[0060] 1) The obtained deviation value e and deviation change rate Perform fuzzification to obtain the fuzzy variable deviation E and deviation change rate E C ;
[0061] 2) According to the deviation e and the deviation change rate e c , combining expert knowledge and operating experience to establish fuzzy rules;
[0062] 3) The input fuzzy variable deviation E and deviation change rate E C Input it into the fuzzy inference machine for inference to get the fuzzy output U;
[0063] 4) Using the maximum value method to defuzzify, converting t...
PUM
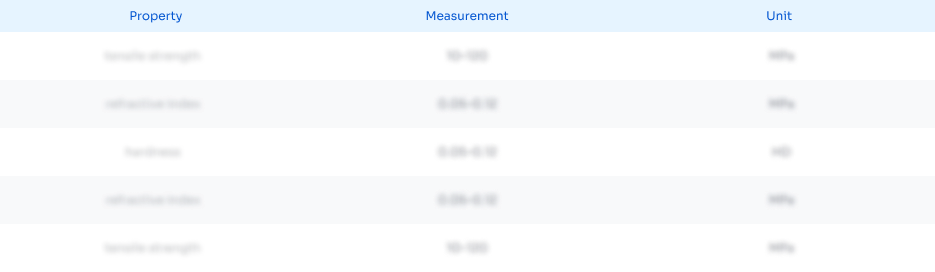
Abstract
Description
Claims
Application Information

- Generate Ideas
- Intellectual Property
- Life Sciences
- Materials
- Tech Scout
- Unparalleled Data Quality
- Higher Quality Content
- 60% Fewer Hallucinations
Browse by: Latest US Patents, China's latest patents, Technical Efficacy Thesaurus, Application Domain, Technology Topic, Popular Technical Reports.
© 2025 PatSnap. All rights reserved.Legal|Privacy policy|Modern Slavery Act Transparency Statement|Sitemap|About US| Contact US: help@patsnap.com