An inspection robot mechanism
A technology of inspection robot and walking mechanism, applied in the direction of overhead line/cable equipment, etc., can solve the problems of complex structure, heavy weight, low efficiency, etc., and achieve the effects of good safety protection, fast obstacle surmounting process, and wide application range
- Summary
- Abstract
- Description
- Claims
- Application Information
AI Technical Summary
Problems solved by technology
Method used
Image
Examples
Embodiment 1
[0043] Such as image 3 As shown, the front opening and closing mechanism 8 includes a first bracket 812, a second bracket 818, a first linkage mechanism, a second linkage mechanism and a linear drive mechanism, wherein the linear drive mechanism is arranged on the front arm 3, The first link mechanism and the second link mechanism are respectively located on both sides of the linear drive mechanism, and are both connected to the front arm 3 and the output end of the linear drive mechanism. The first bracket 812 and One end of the second bracket 818 is respectively connected with the first linkage mechanism and the second linkage mechanism, and the other end of the first bracket 812 and the second bracket 818 is a closed end, and correspondingly, the front traveling mechanism 1 is set on the first bracket 812 or the second bracket 818 close to the closed end, the linear drive mechanism drives the first link mechanism and the second link mechanism on both sides to move, thereby...
Embodiment 2
[0053] Such as Figure 4 As shown, the front opening and closing mechanism 8 includes a first bracket 812, a second bracket 818, a first linkage mechanism, a second linkage mechanism and a linear drive mechanism, wherein the linear drive mechanism is arranged on the front arm 3, The first link mechanism and the second link mechanism are respectively located on both sides of the linear drive mechanism, and are both connected to the front arm 3 and the output end of the linear drive mechanism. The first bracket 812 and One end of the second bracket 818 is respectively connected with the first linkage mechanism and the second linkage mechanism, and the other end of the first bracket 812 and the second bracket 818 is a closed end, and correspondingly, the front traveling mechanism 1 is set on the first bracket 812 or the second bracket 818 close to the closed end, the linear drive mechanism drives the first link mechanism and the second link mechanism on both sides to move, thereb...
PUM
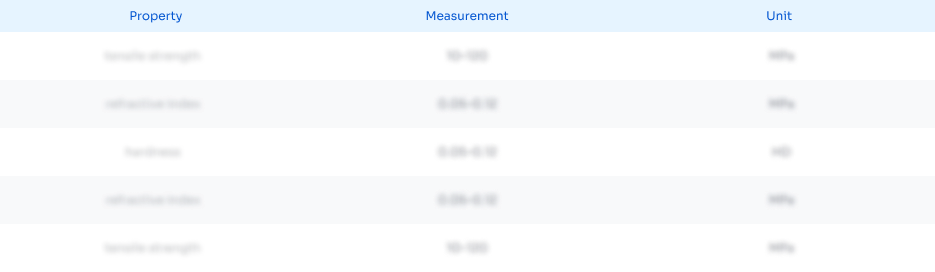
Abstract
Description
Claims
Application Information

- R&D Engineer
- R&D Manager
- IP Professional
- Industry Leading Data Capabilities
- Powerful AI technology
- Patent DNA Extraction
Browse by: Latest US Patents, China's latest patents, Technical Efficacy Thesaurus, Application Domain, Technology Topic, Popular Technical Reports.
© 2024 PatSnap. All rights reserved.Legal|Privacy policy|Modern Slavery Act Transparency Statement|Sitemap|About US| Contact US: help@patsnap.com