A rigidity detection device for a rotary reducer
A technology of rotary reducer and detection device, which is applied in the direction of measuring device, testing of mechanical components, testing of machine/structural components, etc. It can solve the problems of low testing efficiency, inability to meet industrial production and use, and low reliability of test results. Achieve high degree of automation, improve installation efficiency, and ensure installation accuracy
- Summary
- Abstract
- Description
- Claims
- Application Information
AI Technical Summary
Problems solved by technology
Method used
Image
Examples
Embodiment Construction
[0039] The rigidity detection device of the slewing reducer proposed by the present invention will be further described in detail below in conjunction with the accompanying drawings and specific embodiments. Advantages and features of the present invention will be apparent from the following description and claims. It should be noted that all the drawings are in very simplified form and use imprecise ratios, which are only used for the purpose of conveniently and clearly assisting in describing the embodiments of the present invention.
[0040] Such as Figure 4 As shown, the rotary reducer 4 includes a gear transmission structure, a rotary reducer housing 20 and a rotary reducer base 21, such as Figure 1 to Figure 4As shown, the rotary reducer rigidity detection device provided by the present invention includes: a base 1, a connecting seat, a first driving mechanism 9, a second driving mechanism 10, a displacement testing device (not shown in the figure) and a control cente...
PUM
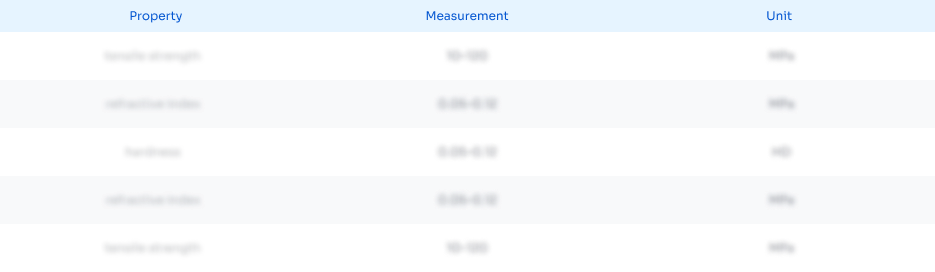
Abstract
Description
Claims
Application Information

- Generate Ideas
- Intellectual Property
- Life Sciences
- Materials
- Tech Scout
- Unparalleled Data Quality
- Higher Quality Content
- 60% Fewer Hallucinations
Browse by: Latest US Patents, China's latest patents, Technical Efficacy Thesaurus, Application Domain, Technology Topic, Popular Technical Reports.
© 2025 PatSnap. All rights reserved.Legal|Privacy policy|Modern Slavery Act Transparency Statement|Sitemap|About US| Contact US: help@patsnap.com