Waste gas incinerator
An incineration device and exhaust gas technology, applied in the direction of incinerators, combustion types, combustion methods, etc., can solve the problems of large temperature fluctuations in the catalytic bed, large internal airflow resistance, switching wind direction, unsuitable for processing concentrated organic waste gas, etc., and achieve good heat capacity and thermal conductivity, less air resistance in the flow channel, and easy installation
- Summary
- Abstract
- Description
- Claims
- Application Information
AI Technical Summary
Problems solved by technology
Method used
Image
Examples
Embodiment 1
[0039] Embodiment 1: as figure 1 As shown, a waste gas incineration device is composed of a furnace 1, a heat storage tube 2, a heater 3, an air inlet 4, an air outlet 5 and a flue gas cooler 8. The upper part of the furnace 1 is provided with an upper sealing end plate 6. The upper sealing end plate 6 and the inner wall of the furnace enclose a sealed space, and a first partition 7 is arranged in the space, and the first partition 7 divides the space into a first upper air passage space 600 (equivalent to the first M upper wind passage spaces, where M=1), the second upper wind passage space 601 (equivalent to the M+1th upper wind passage space, where M=1).
[0040] The lower part of the furnace 1 is provided with a lower sealing end plate 61, which forms a sealed space with the inner wall of the furnace, and a second partition is arranged in the space, and the second partition 71 divides the space into The first lower wind passage space 700 (equivalent to the Lth lower wind ...
Embodiment 2
[0063] Embodiment 2: as figure 2 , image 3 , Figure 4 , Figure 5 : a modular waste gas incinerator, the overall structure is the same as the embodiment. The furnace and the components located in the furnace constitute the main body of the furnace; the main body of the furnace is divided into three modules, including the air inlet and outlet modules (such as figure 2 ), thermal storage modules (such as image 3 ) and heating modules (such as Figure 4 ), the air outlet module, heat storage module and heating module are combined to form the entire furnace body. The air inlet and outlet module is provided with an air inlet 4 and an air outlet 5, and the structure is a square cavity with one side opening; the heat storage module is a square frame with two sides opening, and a plurality of vertical heat storage tubes 2 are arranged inside; The structure of the heating module is a square cavity with an opening on one side, and a heater 3 is arranged inside it. The air inl...
PUM
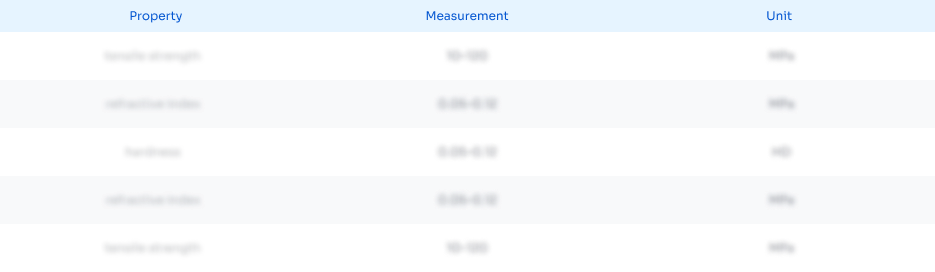
Abstract
Description
Claims
Application Information

- R&D Engineer
- R&D Manager
- IP Professional
- Industry Leading Data Capabilities
- Powerful AI technology
- Patent DNA Extraction
Browse by: Latest US Patents, China's latest patents, Technical Efficacy Thesaurus, Application Domain, Technology Topic, Popular Technical Reports.
© 2024 PatSnap. All rights reserved.Legal|Privacy policy|Modern Slavery Act Transparency Statement|Sitemap|About US| Contact US: help@patsnap.com