Linear linkage telescopic device
A technology of telescopic device and driving device, which is applied in the direction of transmission device, belt/chain/gear, mechanical equipment, etc., can solve the problems that the telescopic speed and telescopic distance are not taken into account at the same time, the number of telescopic sections cannot be adjusted, and the number of sections is fixed, etc. Conducive to mass production, increased telescopic length, easy to install and use
- Summary
- Abstract
- Description
- Claims
- Application Information
AI Technical Summary
Problems solved by technology
Method used
Image
Examples
Embodiment 1
[0040] Such as figure 1 The above is an overall schematic diagram of the linear linkage expansion device of the present invention. The telescopic device in this embodiment is made of two-stage slide blocks. refer to image 3 , Figure 4 and Figure 6 The labels of each structure are: base 1, motor 2-1, motor drive shaft 2-2, transmission gear 2-3, rack 11 on the upper surface of the base, rack 3 on the upper surface of the slider, and rack on the lower surface of the slider 5. Lower slider linkage gear shaft 8, slider lower linkage gear 7, synchronous belt 10, slider upper linkage gear shaft 9, slider upper linkage gear 6, slider upper surface slot 2, slider lower surface slot 4. The guide protrusion 13 on the lower surface of the slider, and the guide groove 12 on the upper surface of the slider.
[0041] The guide projection and the guide groove in this embodiment have trapezoidal cross-sections. Such a design can ensure that the sliding direction of the sliders does n...
Embodiment 2
[0051] A linear linkage telescoping device, comprising a driving device and at least two stages of sliders, the driving device drives the first stage of sliders to slide, characterized in that the sliders of each stage have the same structure and are stacked step by step;
[0052] The upper surfaces of the sliders at all levels are provided with slots 2 on the upper surface and racks 3 on the upper surface along the overall expansion and contraction direction of the device; The lower surface slot 4 and the lower surface rack 5 are provided; the lower surface slot 4 of the slider of this stage is set opposite to the upper surface rack 3 of the upper slider, and the upper surface slot 2 of the slider of the current stage is connected with The rack 5 on the lower surface of the next-level slider is relatively arranged;
[0053] The insides of the sliders at all levels are provided with upper linkage gears 6 that pass through the slots 2 on the upper surface; the interiors of the ...
PUM
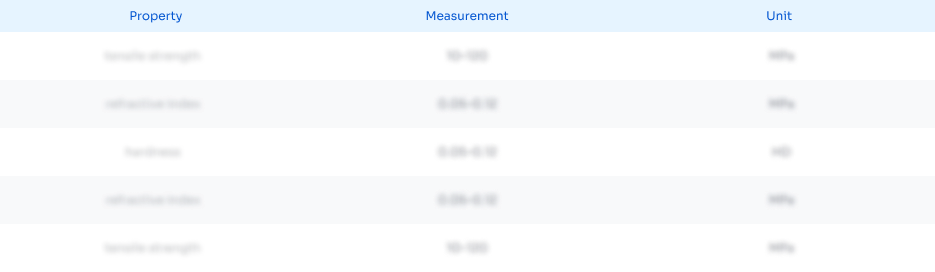
Abstract
Description
Claims
Application Information

- Generate Ideas
- Intellectual Property
- Life Sciences
- Materials
- Tech Scout
- Unparalleled Data Quality
- Higher Quality Content
- 60% Fewer Hallucinations
Browse by: Latest US Patents, China's latest patents, Technical Efficacy Thesaurus, Application Domain, Technology Topic, Popular Technical Reports.
© 2025 PatSnap. All rights reserved.Legal|Privacy policy|Modern Slavery Act Transparency Statement|Sitemap|About US| Contact US: help@patsnap.com