Method for confirming equivalent-groove fullness rate three-phase double-layer stacking sine winding
A double-layer stacked and sinusoidal winding technology, applied in the shape/style/structure of winding conductors, electric components, magnetic circuit shape/style/structure, etc., can solve the problem of harmonic weakening, low winding utilization, and harmonic amplitude Attenuation and other problems, to achieve the effect of harmonic attenuation, improvement of winding utilization, and high fundamental winding coefficient
- Summary
- Abstract
- Description
- Claims
- Application Information
AI Technical Summary
Problems solved by technology
Method used
Image
Examples
Embodiment Construction
[0034] The core of the present invention is to provide a method for determining the three-phase double-layer stacked sinusoidal winding with equal slot full rate. The advantage of the winding is that the fundamental wave winding coefficient of the three-phase double-layer stacked winding sinusoidal winding with equal slot full rate is high, which improves the utilization rate of the winding; in addition, it can effectively weaken most of the harmonics.
[0035] In order to make the purpose, technical solutions and advantages of the embodiments of the present invention clearer, the technical solutions in the embodiments of the present invention will be clearly and completely described below in conjunction with the drawings in the embodiments of the present invention. Obviously, the described embodiments It is a part of embodiments of the present invention, but not all embodiments. Based on the embodiments of the present invention, all other embodiments obtained by persons of or...
PUM
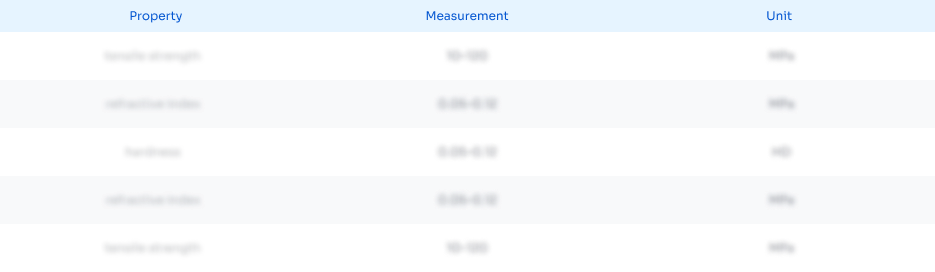
Abstract
Description
Claims
Application Information

- Generate Ideas
- Intellectual Property
- Life Sciences
- Materials
- Tech Scout
- Unparalleled Data Quality
- Higher Quality Content
- 60% Fewer Hallucinations
Browse by: Latest US Patents, China's latest patents, Technical Efficacy Thesaurus, Application Domain, Technology Topic, Popular Technical Reports.
© 2025 PatSnap. All rights reserved.Legal|Privacy policy|Modern Slavery Act Transparency Statement|Sitemap|About US| Contact US: help@patsnap.com