Stable type automatic feeding mechanism
An automatic feeding and stable technology, applied in the direction of conveyor objects, transportation and packaging, etc., can solve the problems of unfavorable wiring and use of sensors, and achieve the effect of improving operation accuracy and stability, convenient operation, and less error-prone
- Summary
- Abstract
- Description
- Claims
- Application Information
AI Technical Summary
Problems solved by technology
Method used
Image
Examples
Embodiment Construction
[0019] The following will clearly and completely describe the technical solutions in the embodiments of the present invention with reference to the accompanying drawings in the embodiments of the present invention. Obviously, the described embodiments are only some, not all, embodiments of the present invention. Based on the embodiments of the present invention, all other embodiments obtained by persons of ordinary skill in the art without creative efforts fall within the protection scope of the present invention.
[0020] refer to Figure 1 to Figure 4 As shown, a stable automatic feeding mechanism includes a fixed base plate 1, on which a first moving assembly 2 moving along the X-axis direction is arranged, and a moving frame 3 is arranged on the first moving assembly, and the moving frame moves along the X-axis A material frame 4 is arranged on the side of the direction, and a second moving assembly 5 moving along the Z-axis direction is arranged between the material frame...
PUM
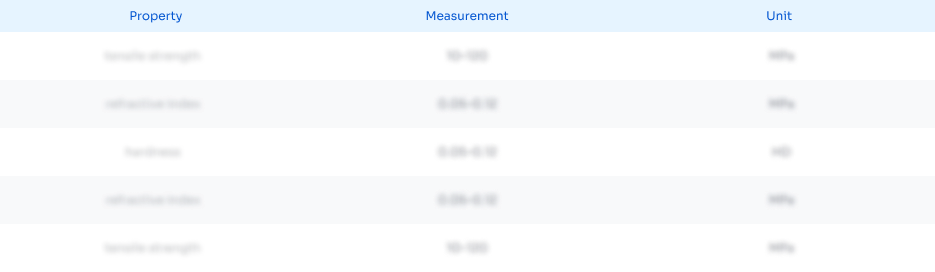
Abstract
Description
Claims
Application Information

- R&D Engineer
- R&D Manager
- IP Professional
- Industry Leading Data Capabilities
- Powerful AI technology
- Patent DNA Extraction
Browse by: Latest US Patents, China's latest patents, Technical Efficacy Thesaurus, Application Domain, Technology Topic, Popular Technical Reports.
© 2024 PatSnap. All rights reserved.Legal|Privacy policy|Modern Slavery Act Transparency Statement|Sitemap|About US| Contact US: help@patsnap.com