A magnetic force control circuit for electromagnetic poles of magnetic suspension bearings based on double bridge structure
A magnetic levitation bearing and magnetic force control technology, applied in high-efficiency power electronic conversion, control/regulation systems, electrical components, etc., can solve problems such as bus voltage short circuit faults, high real-time requirements, and complex control circuits, and reduce on-off losses , The effect of solving the hidden danger of instantaneous short circuit fault of the bus voltage
- Summary
- Abstract
- Description
- Claims
- Application Information
AI Technical Summary
Problems solved by technology
Method used
Image
Examples
Embodiment 1
[0101] Embodiment 1: as Image 6 , a magnetic suspension bearing electromagnetic pole magnetic force control circuit based on a double bridge structure, adopts a main circuit with a double bridge structure, and the main circuit includes 2 power switching devices and 2 diodes: a first power switching device (Q1), a second power switching device (Q1), Two power switching devices (Q2), a first diode (D1) and a second diode (D2);
[0102] The first power switching device and the second diode form a first bridge arm, and the second power switching device and the first diode form a second bridge arm;
[0103] In the first bridge arm, the first terminal of the first power switching device (Q1) is connected to the positive pole of the DC power supply (VDD); the second terminal of the first power switching device is the control terminal, which is connected to the control signal HIN, and the first power The third terminal of the switching device is connected to the negative pole of the...
PUM
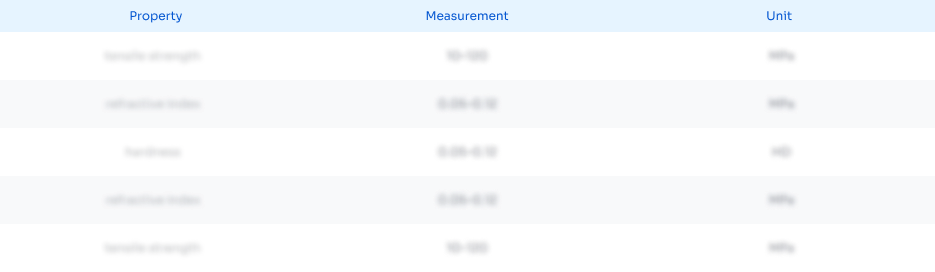
Abstract
Description
Claims
Application Information

- Generate Ideas
- Intellectual Property
- Life Sciences
- Materials
- Tech Scout
- Unparalleled Data Quality
- Higher Quality Content
- 60% Fewer Hallucinations
Browse by: Latest US Patents, China's latest patents, Technical Efficacy Thesaurus, Application Domain, Technology Topic, Popular Technical Reports.
© 2025 PatSnap. All rights reserved.Legal|Privacy policy|Modern Slavery Act Transparency Statement|Sitemap|About US| Contact US: help@patsnap.com