Machining technique for explosion-proof motor end cover
A motor end cover and processing technology technology, applied in the field of explosion-proof motor end cover processing technology, can solve the problem that the special quality requirements of the explosion-proof motor end cover cannot be met, the verticality shape and position accuracy of the end face cannot be guaranteed, and the explosion-proof end cover turning Clamping deformation and other problems, to achieve safe and reliable motor operation, significant energy saving effect, eliminating the effect of turning chatter
- Summary
- Abstract
- Description
- Claims
- Application Information
AI Technical Summary
Problems solved by technology
Method used
Image
Examples
Embodiment 1
[0019] Such as Figure 1~2 As shown, a type 200 explosion-proof motor end cover of ABB in Finland is assembled with the explosion-proof motor shell to form an explosion-proof motor, replacing the traditional ordinary motor. The material of the end cover is gray iron HT200, and it is required to process a large end face 2 diameter tolerance +0.3 -0.1 , Perpendicularity 0.1, coaxiality ∮ 0.1, notch depth 26.5, to ensure the assembly requirements of explosion-proof motors.
[0020] 1) Use a three-jaw chuck to clamp and align the blank, the outer circle of the car is 1, the diameter of the outer circle 1 is controlled to ∮287±0.5, and the depth is 7±0.5.
[0021] 2) Using a C630 lathe, locate the end face of the outer circle 1, align and clamp the outer circle 1, turn the big end face 2 and the big face 3, and control the diameter of the big end face 3 ∮334.8 +0.3 -0.1 , depth tolerance 26.5±0.2, large face 3 diameter ∮174.2 +0.1 -0.3 .
[0022] 3) Using a C630 lathe, locat...
Embodiment 2
[0028] A type 225 explosion-proof motor end cover of ABB in Finland, which is assembled with an explosion-proof motor casing to form an explosion-proof motor, replacing the traditional ordinary motor. The material of the end cover is gray iron HT200, and it is required to process a large end face with a diameter tolerance of 2. +0.3 -0.1 , Perpendicularity 0.1, coaxiality ∮ 0.1, notch depth 26.5, to ensure the assembly requirements of explosion-proof motors.
[0029] 1) Use a three-jaw chuck to clamp and align the blank, the outer circle of the car is 1, the control is ∮311±0.5, and the depth is 9±0.5.
[0030] 2) Use a C630 lathe to locate the end face of the outer circle, align and clamp the outer circle 1, turn the big end face seam 2 and the large face hole 3, and the diameter of the large end face seam 2 is ∮376.8 +0.3 -0.1 , depth tolerance 26.5±0.2, large face 3 diameter ∮200.2 +0.1 -0.3 .
[0031] 3) Using a C630 lathe, locate the seam 2 of the large end face, cla...
Embodiment 3
[0037] A type 250 explosion-proof motor end cover of ABB in Finland, which is assembled with an explosion-proof motor casing to form an explosion-proof motor, replacing the traditional ordinary motor. The material of the end cover is gray iron HT200, and it is required to process a large diameter tolerance of the end face. +0.3 -0.1 , Perpendicularity 0.1, coaxiality ∮ 0.1, notch depth 26.5, to ensure the assembly requirements of explosion-proof motors.
[0038] 1) Use a three-jaw chuck to clamp and align the blank, turn the outer circle, control ∮350±0.5, and the depth dimension is 9±0.5.
[0039] 2) Use a C630 lathe to locate the end face of the outer circle, align and clamp the outer circle, turn the big end face 2 and the big face 3, and the diameter of the big end face 2 is ∮424.8 +0.3 -0.1 , depth tolerance 26.5±0.2, large face 3 diameter ∮209.2 +0.1 -0.3 .
[0040] 3) Using a C630 lathe, locate the seam 2 of the large end face, clamp and align, turn the small face ...
PUM
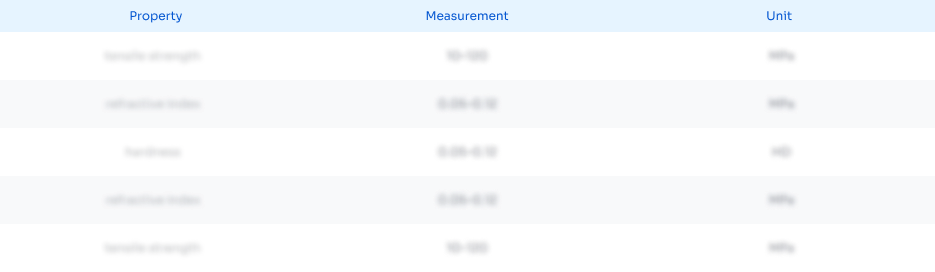
Abstract
Description
Claims
Application Information

- R&D
- Intellectual Property
- Life Sciences
- Materials
- Tech Scout
- Unparalleled Data Quality
- Higher Quality Content
- 60% Fewer Hallucinations
Browse by: Latest US Patents, China's latest patents, Technical Efficacy Thesaurus, Application Domain, Technology Topic, Popular Technical Reports.
© 2025 PatSnap. All rights reserved.Legal|Privacy policy|Modern Slavery Act Transparency Statement|Sitemap|About US| Contact US: help@patsnap.com