Wing interior supporting structure of unmanned aerial vehicle
An internal support, UAV technology, applied in the direction of wings, unmanned aerial vehicles, motor vehicles, etc., can solve the influence of wing rudder surface effect, increased tremor, and increased influence of UAV flight stability, etc. problem, to achieve the effect of ensuring flight stability and flight speed, and reducing tremor
- Summary
- Abstract
- Description
- Claims
- Application Information
AI Technical Summary
Problems solved by technology
Method used
Image
Examples
Embodiment 1
[0050] figure 1 It is a top view of Embodiment 1 of the present invention, figure 2 It is the left side view of Embodiment 1 of the present invention, image 3 It is a schematic diagram of a fuselage connector part according to an embodiment of the present invention, Figure 4It is a schematic diagram of the connecting baffle part of the present invention, as shown in the figure: a kind of unmanned aerial vehicle wing internal support structure, including front beam 1, rear beam 2, connecting baffle plate 5 and 6 support plates 6; the front beam 1 includes a front beam outer bar 11 and a front beam inner bar 12, and a beam connector 3 is provided between the front beam outer bar 11 and the front beam inner bar 12; the rear beam 2 includes a rear beam outer bar 22 and a rear beam The inner rod 21, the outer rod 22 of the rear beam and the inner rod 21 of the rear beam are provided with a beam connector 3; the inner rod 12 of the front beam includes a metal rod 111 of the inn...
Embodiment 2
[0059] Figure 4 It is a schematic diagram of the connecting baffle part of the present invention, Figure 5 It is a top view of Embodiment 2 of the present invention, Figure 6 It is the left view of Embodiment 2 of the present invention, Figure 7 It is a schematic diagram of the support plate part of the second embodiment of the present invention, as shown in the figure: an internal support structure of an unmanned aerial vehicle wing, including a front beam 1, a rear beam 2, a connecting baffle 5 and 8 support plates 6; The front beam 1 includes a front beam outer bar 11 and a front beam inner bar 12, and a beam connector 3 is arranged between the front beam outer bar 11 and the front beam inner bar 12; the rear beam 2 includes a rear beam outer bar 22 and the rear beam inner rod 21, the rear beam outer rod 22 and the rear beam inner rod 21 are provided with a beam connector 3; the front beam inner rod 12 includes a front beam inner rod metal rod 121 and a front beam inn...
PUM
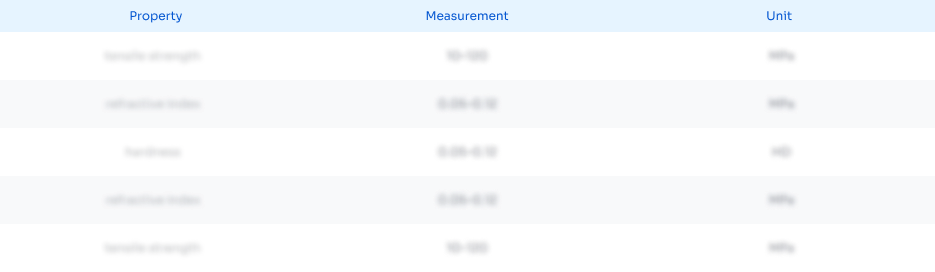
Abstract
Description
Claims
Application Information

- Generate Ideas
- Intellectual Property
- Life Sciences
- Materials
- Tech Scout
- Unparalleled Data Quality
- Higher Quality Content
- 60% Fewer Hallucinations
Browse by: Latest US Patents, China's latest patents, Technical Efficacy Thesaurus, Application Domain, Technology Topic, Popular Technical Reports.
© 2025 PatSnap. All rights reserved.Legal|Privacy policy|Modern Slavery Act Transparency Statement|Sitemap|About US| Contact US: help@patsnap.com