Plate pressing device, continuous feeding system and continuous vertical electroplating production line
A technology of feeding system and pressing plate, applied in circuits, electrical components, electrolysis process, etc., can solve the problems of continuous feeding affecting the feeding system, inability to complete plate changing, and long plate changing process, etc., and achieve the effect of increasing buffer time.
- Summary
- Abstract
- Description
- Claims
- Application Information
AI Technical Summary
Problems solved by technology
Method used
Image
Examples
Embodiment 1
[0070] Such as figure 1 As shown, this embodiment provides a pressing plate device, including
[0071] Riser 61 is arranged on the horizontal platform;
[0072] At least two platen parts 62 are respectively movably arranged on the vertical plate 61, and respectively form a board-passing space with the vertical plate 61;
[0073] The driving device 63 is used to drive the platen member 62 to change the size of the plate-passing space.
[0074] In the pressing plate device with the above structure, when it is necessary to connect two rolls of substrates, the driving device 63 drives at least one platen member 62 to move towards the direction of the vertical plate 61 to press the end of the previous roll of substrates located in the passing space on the surface of the vertical plate 61; At least another platen member 62 moves towards the direction of the vertical plate 61, and presses the starting end of the subsequent roll of substrates located in the passing plate space on th...
Embodiment 2
[0088] Such as figure 2 As shown, the present embodiment provides a continuous feeding system, comprising
[0089] Rack 1;
[0090] At least one feeding shaft 2 is arranged vertically on the horizontal platform of the frame 1, capable of rotating in the horizontal direction and moving up and down in the vertical direction, and is used for sheathing the substrate roll;
[0091] The pressing plate device 6 is used for passing the substrate, and pressing the first and last ends of two adjacent rolls of the substrate from the feeding shaft 2;
[0092] The connecting plate structure is used to connect the first and last ends of two adjacent rolls of substrates together during the pressing of the first and last ends of two adjacent rolls of substrates by the pressing plate device 6;
[0093] The transfer device is arranged between the feeding shaft 2 and the electroplating tank, and is used to transfer the substrate coming out of the feeding shaft 2 into the electroplating tank t...
Embodiment 3
[0132] This embodiment provides a continuous vertical electroplating production line, comprising
[0133] Feeding system for continuous output of substrates;
[0134] The electroplating device has an electroplating tank and a conveying mechanism, and is used for electroplating the substrate input into the electroplating tank by the feeding system;
[0135] The receiving system is used to continuously collect the substrates conveyed out of the electroplating tank into rolls;
[0136] Feeding system is any continuous conveying system described in embodiment 2.
[0137] The continuous vertical electroplating production line of the above structure adopts any one of the continuous feeding systems recorded in embodiment 2, so that when the electroplating production line does not stop in the electroplating tank, the time for changing plates is shortened, and the buffer time of the plate changing process is increased simultaneously. Improve the efficiency of plate change, so as to r...
PUM
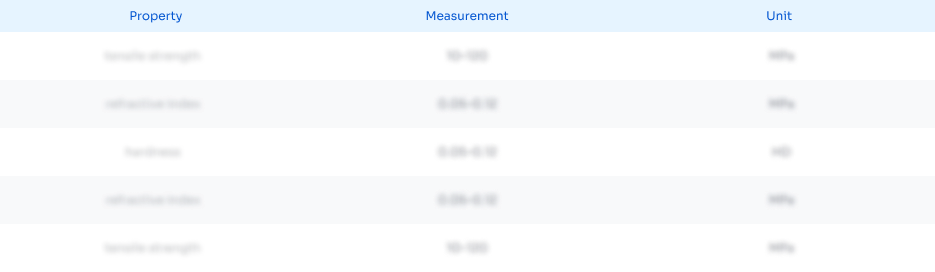
Abstract
Description
Claims
Application Information

- R&D Engineer
- R&D Manager
- IP Professional
- Industry Leading Data Capabilities
- Powerful AI technology
- Patent DNA Extraction
Browse by: Latest US Patents, China's latest patents, Technical Efficacy Thesaurus, Application Domain, Technology Topic, Popular Technical Reports.
© 2024 PatSnap. All rights reserved.Legal|Privacy policy|Modern Slavery Act Transparency Statement|Sitemap|About US| Contact US: help@patsnap.com