Decoupled internal model controller, control system and control method for multivariable time-delay non-minimum-phase non-square systems
A non-minimum phase, internal model controller technology, applied in general control systems, program control, adaptive control, etc., can solve problems such as difficult adjustment, achieve easy implementation, improve anti-disturbance performance and fast anti-disturbance response ability, Enhanced Robustness Effects
- Summary
- Abstract
- Description
- Claims
- Application Information
AI Technical Summary
Problems solved by technology
Method used
Image
Examples
Embodiment Construction
[0028] The present invention will be specifically described below in conjunction with the accompanying drawings and specific embodiments.
[0029] At present, the multivariable control method based on the internal model control method has produced a variety of design methods, and the decoupling control method of the multivariable system is divided into static decoupling and dynamic decoupling. At present, the static decoupling method is mainly used for the decoupling of non-square controlled objects, and the internal model controller is designed at the steady-state point. This method is simple to design a decoupler and has a fast response speed, but it does not take into account the dynamics of the controlled object. Performance, dynamic decoupling effects are limited, and it is not suitable for plants with right-half-plane (RHP) zeros. For non-square controlled objects containing RHP zeros, K.L.N.SARMA et al. extended the static decoupling method to non-square controlled obje...
PUM
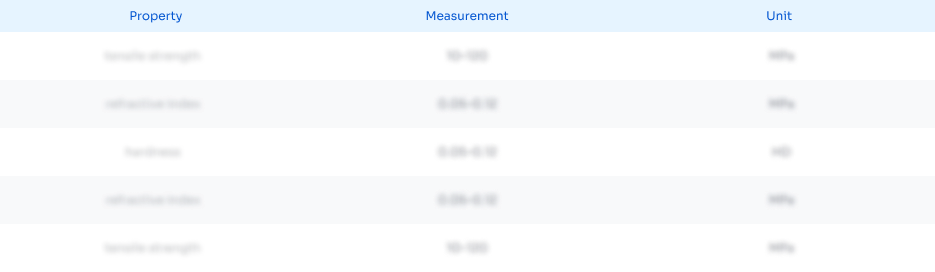
Abstract
Description
Claims
Application Information

- R&D
- Intellectual Property
- Life Sciences
- Materials
- Tech Scout
- Unparalleled Data Quality
- Higher Quality Content
- 60% Fewer Hallucinations
Browse by: Latest US Patents, China's latest patents, Technical Efficacy Thesaurus, Application Domain, Technology Topic, Popular Technical Reports.
© 2025 PatSnap. All rights reserved.Legal|Privacy policy|Modern Slavery Act Transparency Statement|Sitemap|About US| Contact US: help@patsnap.com