Wheel beam type axle-free frame manufactured by 3D printing
A 3D printing and wheel-beam technology, which is applied in vehicle parts, substructure, transportation and packaging, etc., can solve problems such as failure to realize electrification, light weight, intelligence, and failure to realize bridgeless new structure , to achieve the effect of convenient innovation, high rigidity and short production cycle
- Summary
- Abstract
- Description
- Claims
- Application Information
AI Technical Summary
Problems solved by technology
Method used
Image
Examples
Embodiment approach 1
[0038] Implementation mode one: if figure 1 , figure 2 and image 3 As shown, the whole is composed of two parts, a connecting support frame 1 and a front and rear wheel beam frame 2, and there is only a chassis frame without a base plate 3 and a vehicle body 4.
Embodiment approach 2
[0039] Implementation mode two: if Figure 5 As shown, the whole is composed of three parts, the connecting support frame 1, the front and rear wheel beam frames 2 and the bottom plate 3, and the bottom plate 3 is added on the basis of the first embodiment.
Embodiment approach 3
[0040] Implementation mode three: if Figure 6 As shown, the whole is composed of four parts, the connecting support frame 1, the front and rear wheel beam frames 2, the bottom plate 3 and the vehicle body 4, and the vehicle body 4 is added on the basis of the second embodiment.
PUM
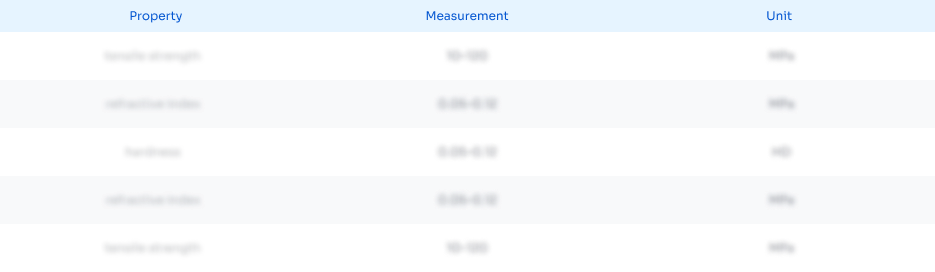
Abstract
Description
Claims
Application Information

- R&D
- Intellectual Property
- Life Sciences
- Materials
- Tech Scout
- Unparalleled Data Quality
- Higher Quality Content
- 60% Fewer Hallucinations
Browse by: Latest US Patents, China's latest patents, Technical Efficacy Thesaurus, Application Domain, Technology Topic, Popular Technical Reports.
© 2025 PatSnap. All rights reserved.Legal|Privacy policy|Modern Slavery Act Transparency Statement|Sitemap|About US| Contact US: help@patsnap.com