Modular robot self-repairing simulation system and method
A technology of a robot system and a simulation system is applied in the field of self-repairing simulation systems of modular robots to save time and manpower, improve work efficiency, and facilitate data processing.
- Summary
- Abstract
- Description
- Claims
- Application Information
AI Technical Summary
Problems solved by technology
Method used
Image
Examples
Embodiment Construction
[0065] The present invention will be described in detail below in conjunction with specific embodiments. The following examples will help those skilled in the art to further understand the present invention, but do not limit the present invention in any form. It should be noted that those skilled in the art can make several modifications and improvements without departing from the concept of the present invention. These all belong to the protection scope of the present invention.
[0066] like figure 1 As shown, a modular robot self-repair simulation system is composed of multiple modules, including: robot control platform 1, robot self-repair simulation platform 2, fault generation and analysis platform 3, wherein:
[0067] The robot control platform 1 is connected with the physical robot system for controlling the robot;
[0068] The robot self-repair simulation platform 2 is connected to the robot control platform 1 to perform self-repair simulation and transmit simulati...
PUM
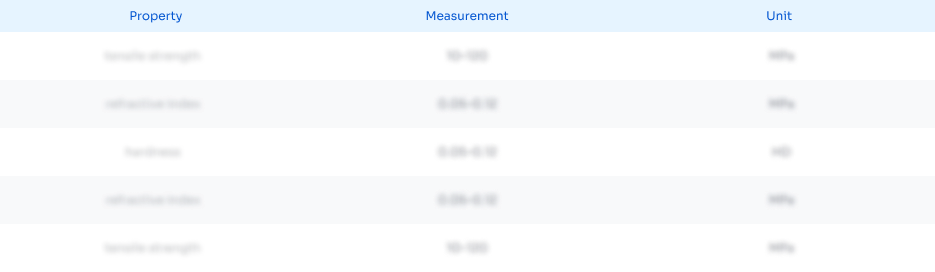
Abstract
Description
Claims
Application Information

- R&D
- Intellectual Property
- Life Sciences
- Materials
- Tech Scout
- Unparalleled Data Quality
- Higher Quality Content
- 60% Fewer Hallucinations
Browse by: Latest US Patents, China's latest patents, Technical Efficacy Thesaurus, Application Domain, Technology Topic, Popular Technical Reports.
© 2025 PatSnap. All rights reserved.Legal|Privacy policy|Modern Slavery Act Transparency Statement|Sitemap|About US| Contact US: help@patsnap.com