A kind of magnesium alloy metallographic etchant
A technology of corrosive agent and magnesium alloy, which is applied in the field of metallographic test of magnesium alloy, can solve the problems of poor corrosion resistance, blurred surface, and difficult identification of the second phase of magnesium alloy, achieve accurate corrosion time, good effect, and shorten corrosion time Effect
- Summary
- Abstract
- Description
- Claims
- Application Information
AI Technical Summary
Problems solved by technology
Method used
Examples
Embodiment 1
[0015] The magnesium alloy metallographic etchant of this embodiment is composed of the following components: 1 mL of nitric acid with a concentration of 68% by mass, 15 g of oxalic acid, 4 mL of acetic acid with a concentration of 98% by mass, and 100 mL of ethanol.
[0016] Add 100mL of ethanol into a beaker, add 1mL of nitric acid with a concentration of 68% by mass, 15g of oxalic acid, and 4mL of acetic acid with a concentration of 98% by mass, stir and mix evenly to obtain a magnesium alloy metallographic etchant.
[0017] Immerse the polished magnesium alloy sample in the magnesium alloy metallographic etchant prepared above, etch for 5 seconds, take it out, wash it with ethanol, and dry it in the air to obtain the corroded magnesium alloy sample.
Embodiment 2
[0019] The magnesium alloy metallographic etchant of this embodiment is composed of the following components: 2 mL of nitric acid with a concentration of 68% by mass, 12 g of oxalic acid, 3 mL of acetic acid with a concentration of 98% by mass, and 100 mL of ethanol.
[0020] Add 100mL of ethanol into a beaker, add 2mL of nitric acid with a concentration of 68% by mass, 12g of oxalic acid, and 3mL of acetic acid with a concentration of 98% by mass, stir and mix evenly to obtain a magnesium alloy metallographic etchant.
[0021] The polished magnesium alloy sample was immersed in the prepared magnesium alloy metallographic etchant, etched for 7s, taken out, rinsed with ethanol, and dried in air to obtain the corroded magnesium alloy sample.
Embodiment 3
[0023] The magnesium alloy metallographic etchant of this embodiment is composed of the following components: 3 mL of nitric acid with a concentration of 68% by mass, 10 g of oxalic acid, 2 mL of acetic acid with a concentration of 98% by mass, and 100 mL of ethanol.
[0024] Add 100mL of ethanol into a beaker, add 3mL of nitric acid with a concentration of 68% by mass, 10g of oxalic acid, and 2mL of acetic acid with a concentration of 98% by mass, stir and mix evenly to obtain a magnesium alloy metallographic etchant.
[0025] The polished magnesium alloy sample was immersed in the prepared magnesium alloy metallographic etchant, etched for 10 seconds, taken out, rinsed with ethanol, and dried with filter paper to obtain the corroded magnesium alloy sample.
[0026] The corrosion time of the magnesium alloy metallographic etchant of the present invention is short, and the corrosion time of using the magnesium alloy metallographic etchant of the present invention only needs 5-1...
PUM
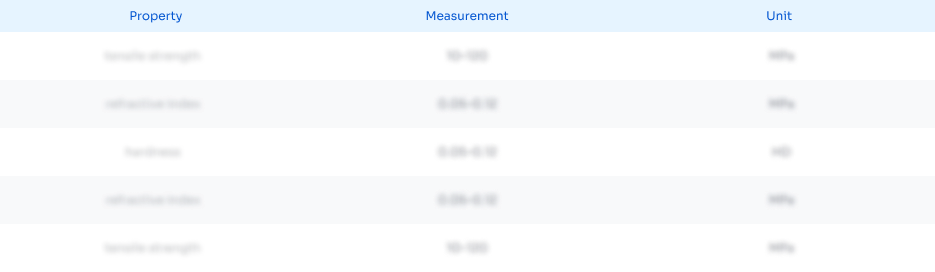
Abstract
Description
Claims
Application Information

- R&D
- Intellectual Property
- Life Sciences
- Materials
- Tech Scout
- Unparalleled Data Quality
- Higher Quality Content
- 60% Fewer Hallucinations
Browse by: Latest US Patents, China's latest patents, Technical Efficacy Thesaurus, Application Domain, Technology Topic, Popular Technical Reports.
© 2025 PatSnap. All rights reserved.Legal|Privacy policy|Modern Slavery Act Transparency Statement|Sitemap|About US| Contact US: help@patsnap.com