Rotating motor
A technology for rotating electrical machines and rotating shafts, applied to electrical components, electromechanical devices, electrical components, etc., can solve the problem of inability to cool the rotor 72, and achieve the effect of suppressing insufficient supply and reducing supply pressure
- Summary
- Abstract
- Description
- Claims
- Application Information
AI Technical Summary
Problems solved by technology
Method used
Image
Examples
no. 1 approach
[0077] 1. Description of the overall structure
[0078] [1-1. Overall structure]
[0079] figure 1 It is a partial cross-sectional view showing a vehicle 10 mounted with a motor 12 as a rotating electric machine according to the first embodiment of the present invention focusing on a cooling system (refrigerant supply mechanism). figure 2 It is a partially enlarged cross-sectional view showing the flow of the cooling oil 42 in the motor 12 of the first embodiment. exist figure 2 In , thick arrows of solid lines, dashed lines, and one-dot chain lines (however, except for the lead-out lines for reference symbols) indicate the flow of the cooling oil 42 . That is, the arrows of the solid line indicate the flow of the cooling oil 42 supplied from the side cover 30 (described later) and the flow of the cooling oil 42 supplied into the rotating shaft 50 . The dotted arrows indicate the flow of the cooling oil 42 passing through or after passing through the first through holes...
no. 2 approach
[0149] 1. Explanation of overall structure (differences from the first embodiment)
[0150] In the second embodiment, the shape of the cylindrical member 52a is different from that of the cylindrical member 52 of the first embodiment. Components that are the same as those in the first embodiment are denoted by the same reference numerals and description thereof will be omitted.
[0151] Figure 14 It is a partial enlarged cross-sectional view showing the flow of the cooling oil 42 in the motor 12a of the second embodiment. exist Figure 14 In , arrows of solid lines, dashed lines, and one-dot chain lines (however, the lead-out lines for reference symbols are excluded.) indicate the flow of the cooling oil 42 . That is, the arrows of the solid line indicate the flow of the cooling oil 42 supplied from the side cover 30 and the flow of the cooling oil 42 supplied into the rotating shaft 50 . The dotted arrows indicate the flow of the cooling oil 42 passing through or after p...
PUM
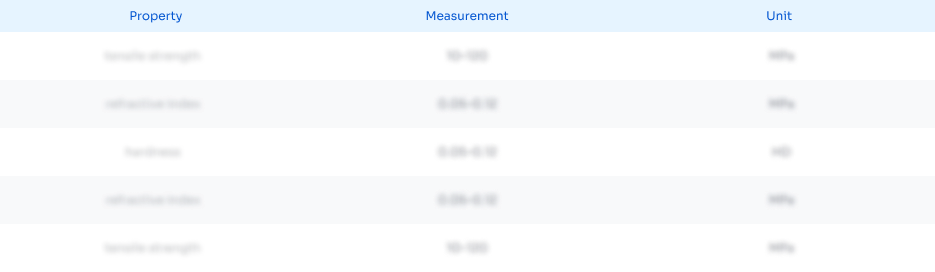
Abstract
Description
Claims
Application Information

- R&D Engineer
- R&D Manager
- IP Professional
- Industry Leading Data Capabilities
- Powerful AI technology
- Patent DNA Extraction
Browse by: Latest US Patents, China's latest patents, Technical Efficacy Thesaurus, Application Domain, Technology Topic, Popular Technical Reports.
© 2024 PatSnap. All rights reserved.Legal|Privacy policy|Modern Slavery Act Transparency Statement|Sitemap|About US| Contact US: help@patsnap.com