Front wiring case with front panel capable of overturning up and down
A front panel, front wiring technology, applied in the direction of cabinet/cabinet/drawer parts, etc., can solve problems such as increasing cost, reducing efficiency, and shaking
- Summary
- Abstract
- Description
- Claims
- Application Information
AI Technical Summary
Problems solved by technology
Method used
Image
Examples
Embodiment Construction
[0021] The following describes the present invention in detail with reference to the drawings and specific embodiments.
[0022] A front wiring chassis with a front panel turned upside down, comprising: a chassis body, a turning device connected to the chassis body and used for fixing the front panel, and an automatic locking device connected to the turning device and fixed on the chassis body for positioning the front panel, The turning device consists of a turning bracket that is rotatably connected to the chassis body on one side and fixed to the front panel, fixed on both sides of the chassis body and used to fix the turning bracket, and connected to a connecting rod assembly between the turning bracket and the fixing member. The connecting rod assembly is composed of a connecting rod that is rotatably connected to the turning bracket, and a rocker that is rotatably connected between the fixing part and the connecting rod. The fixing piece is provided with a slot hole that is...
PUM
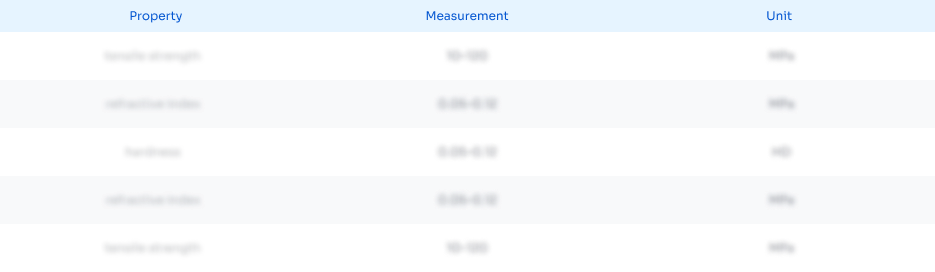
Abstract
Description
Claims
Application Information

- R&D Engineer
- R&D Manager
- IP Professional
- Industry Leading Data Capabilities
- Powerful AI technology
- Patent DNA Extraction
Browse by: Latest US Patents, China's latest patents, Technical Efficacy Thesaurus, Application Domain, Technology Topic, Popular Technical Reports.
© 2024 PatSnap. All rights reserved.Legal|Privacy policy|Modern Slavery Act Transparency Statement|Sitemap|About US| Contact US: help@patsnap.com