Multi-working-condition bridge detecting vehicle
A bridge inspection vehicle and multi-working-condition technology, which is applied to bridges, bridge parts, bridge construction, etc., can solve problems such as construction delays, manpower loss in disassembling and assembling sound insulation walls, and non-adjustable spanning ability, so as to achieve high capacity improvement and realize The effect of breadth capability
- Summary
- Abstract
- Description
- Claims
- Application Information
AI Technical Summary
Problems solved by technology
Method used
Image
Examples
Embodiment Construction
[0022] The present invention will be further described below in conjunction with drawings and embodiments.
[0023] Such as figure 1 As shown, a multi-working condition bridge inspection vehicle of the present invention includes a chassis 1, a first slewing mechanism 4, an overturning mechanism 6, a lifting cylinder 7, a vertical arm 8, a second slewing support 9, a second slewing mechanism 10 and a telescopic arm 11;
[0024] The chassis 1 provides a carrier for the working device of the bridge inspection vehicle; at the same time, the power of the chassis engine can be sent to the working device as the source power through the power output of the chassis engine.
[0025] A subframe 2 is installed on the chassis 1, and a first slewing bearing 3 is installed on the subframe 2. The subframe 2 bears the part above the first slewing bearing 3, and transmits its force to the girder of the chassis 1. It also provides space for the arrangement of other accessories of the vehicle. ...
PUM
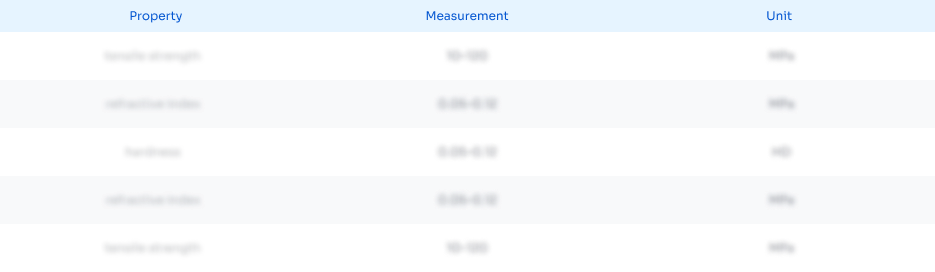
Abstract
Description
Claims
Application Information

- R&D
- Intellectual Property
- Life Sciences
- Materials
- Tech Scout
- Unparalleled Data Quality
- Higher Quality Content
- 60% Fewer Hallucinations
Browse by: Latest US Patents, China's latest patents, Technical Efficacy Thesaurus, Application Domain, Technology Topic, Popular Technical Reports.
© 2025 PatSnap. All rights reserved.Legal|Privacy policy|Modern Slavery Act Transparency Statement|Sitemap|About US| Contact US: help@patsnap.com