A method for monitoring and adjusting the liquid level stability of etching tank
An etching tank and stability technology, applied in electrical components, circuits, semiconductor/solid-state device testing/measurement, etc., can solve problems such as liquid level gradient or poor liquid level stability, irregular etching and debugging results, etc. To achieve the effect of convenient observation and reading, speeding up the adjustment speed
- Summary
- Abstract
- Description
- Claims
- Application Information
AI Technical Summary
Problems solved by technology
Method used
Image
Examples
Embodiment 1
[0025] This embodiment provides a method for monitoring and adjusting the liquid level stability of the etching tank, which includes the following steps in sequence:
[0026] (a) Select two test points A and B at different positions of the etching tank, and respectively place the first liquid level gauge 9 and the second liquid level gauge 10 at the test points (the first liquid level gauge 9 and the second liquid level gauge The liquid level gauge 10 is made of acid and alkali-resistant Teflon transparent material, with a diameter of 5mm~20mm and a minimum scale of 0.5mm, which is conducive to prolonging the service life on the one hand and precise control on the other hand). The standard liquid level height Hs at the two test points when the state is stable A 、H sB And the standard liquid level tolerance ΔH of the test point s , the standard liquid level tolerance ΔH of the etching equipment is used in this embodiment s =2mm;
[0027] (b) Start the etching equipment so t...
PUM
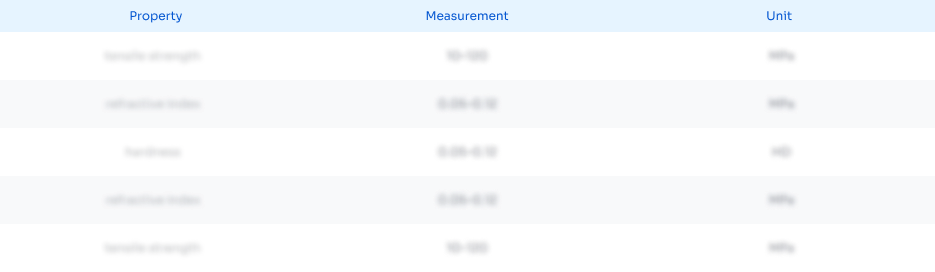
Abstract
Description
Claims
Application Information

- R&D
- Intellectual Property
- Life Sciences
- Materials
- Tech Scout
- Unparalleled Data Quality
- Higher Quality Content
- 60% Fewer Hallucinations
Browse by: Latest US Patents, China's latest patents, Technical Efficacy Thesaurus, Application Domain, Technology Topic, Popular Technical Reports.
© 2025 PatSnap. All rights reserved.Legal|Privacy policy|Modern Slavery Act Transparency Statement|Sitemap|About US| Contact US: help@patsnap.com