Rope counterweight sun wing auxiliary turning mechanism
A flipping mechanism and solar technology, applied in aerospace equipment, simulators of space navigation conditions, transportation and packaging, etc., can solve the problem that the solar wing drive mechanism does not have the ability to expand and retract, and achieve simple structure and easy operation Effect
- Summary
- Abstract
- Description
- Claims
- Application Information
AI Technical Summary
Problems solved by technology
Method used
Image
Examples
specific Embodiment approach 1
[0030] Specific implementation mode one: combine Figure 1 to Figure 10 Describe this embodiment. This embodiment includes a vertical carriage 1, a driving mechanism 2, a magnet 3, a counterweight mechanism 4, a solar wing 5, a horizontal carriage 7, a guide rail 8, a connector 9, a solar wing wire rope 10, and a lock 11, lock pin 12 and bearing 13,
[0031] The vertical carriage 1 comprises a connecting plate 1-1, a front channel plate 1-2, a rear channel plate 1-3 and four connecting elements 1-5, and the front channel plate 1-2 and the rear channel plate 1- 3 Arranged back to back, four vertical slotted holes 1-4 are arranged on the front slotted plate 1-2 and the rear slotted plate 1-3, the four vertical slotted holes 1-4 are arranged in a rectangle, the front slotted plate 1 -2 is connected with the four connection elements 1-5 adopted by the rear channel plate 1-3, each connection element 1-5 is arranged in the corresponding vertical slot 1-4, and the connection plate 1...
specific Embodiment approach 2
[0038] Specific implementation mode two: combination figure 1 , figure 2 and Figure 11To describe this embodiment, when the driving mechanism 2 of this embodiment is located on the left side of the slideway 7-1, when the first angle α between the solar blade 5 and the horizontal line is 15°-25°, the solar blade 5 is in a folded state, See Figure 11 . Other components and connections are the same as those in the first embodiment.
specific Embodiment approach 3
[0039] Specific implementation mode three: combination figure 1 , figure 2 and Figure 11 Describe this embodiment, when the driving mechanism 2 of this embodiment is located on the left side of the slideway 7-1, when the first angle α between the solar blade 5 and the horizontal line is 20°, the optimal angle of the sun blade 5 is in the folded state ,See Figure 11 . Other components and connections are the same as those in the second embodiment.
PUM
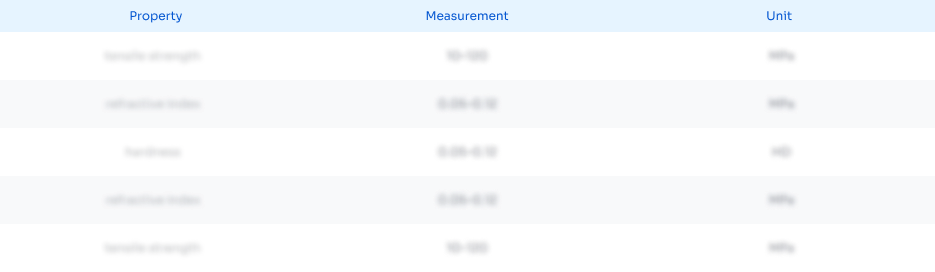
Abstract
Description
Claims
Application Information

- Generate Ideas
- Intellectual Property
- Life Sciences
- Materials
- Tech Scout
- Unparalleled Data Quality
- Higher Quality Content
- 60% Fewer Hallucinations
Browse by: Latest US Patents, China's latest patents, Technical Efficacy Thesaurus, Application Domain, Technology Topic, Popular Technical Reports.
© 2025 PatSnap. All rights reserved.Legal|Privacy policy|Modern Slavery Act Transparency Statement|Sitemap|About US| Contact US: help@patsnap.com