Method for producing multicolor section color yarn and drawing frame device
A drawing frame and color yarn technology, applied in textiles and papermaking, etc., can solve the problems of complex equipment, high cost, easy quality problems, etc., and achieve the effect of simple equipment and convenient production and operation.
- Summary
- Abstract
- Description
- Claims
- Application Information
AI Technical Summary
Problems solved by technology
Method used
Image
Examples
Embodiment 1
[0068] The main color roving adopts white raw cotton, and the roving quantitative adopts 5.2g / 10m. The auxiliary color roving is made of dyed red cotton and blue cotton. After each process of cleaning, carding, and pre-drawing, red pre-drawing frames and blue pre-drawing frames are produced.
[0069] Secondly, in the drawing process, the process of 4A+4B is adopted, 4 red slivers and 4 blue slivers are fed into the cotton feeding roller in parallel at the same time, and the 4 red slivers are concentrated on the cotton guide plate when they are fed. When feeding, the 4 blue slivers are concentrated on the other side of the cotton guide plate, and finally the cross-sectional effect of the auxiliary color roving is formed. figure 1 As shown, the basis weight of the combined sliver is 20.5 grams per 5 meters.
[0070] Then, on the traditional roving machine equipment, the auxiliary color roving is spun, the roving basis weight is 5.2 g / 10 m, and the roving twist is 51 twists / m. ...
Embodiment 2
[0075] The main color roving adopts white raw cotton, and the main color roving adopts 5.2 g / 10 meters. The auxiliary color roving is made of dyed red cotton, blue cotton, and yellow cotton. After each process of blowing, carding, and pre-drawing, red pre-drawing frames, blue pre-drawing frames and yellow pre-drawing frames are produced.
[0076] Then, in the drawing process, the 2A+2B+2C process is adopted, that is, 2 red pre-draw frames, 2 blue pre-draw frames and 2 yellow pre-draw frames are simultaneously fed to the cotton feeder in parallel, and the same color pre-draw frames are used. The drawing frames are concentrated on the cotton guide plate, specifically, an elliptical cylindrical additional spacer device is installed on the cotton guide plate between 2 red pre-draw frames, 2 blue pre-draw frames and 2 yellow pre-draw frames , After the drawing process, it is made into cooked strips with three colors, and the quantitative use of cooked strips is 20.5 grams / 5 meters....
Embodiment 3
[0083] The main color roving adopts white raw cotton, and the roving quantitative adopts 5.2g / 10m. The auxiliary color roving is made of dyed red cotton, blue cotton, yellow cotton, and green cotton. After each process of cleaning, carding, and pre-combining, red pre-drawing frames, blue pre-drawing frames, and yellow pre-drawing frames are produced. bar and green pre-draw.
[0084] Then, in the drawing process, the process of 2A+2B+2C+2D is adopted, that is, 2 red pre-draw frames, 2 blue pre-draw frames, 2 yellow pre-draw frames and 2 green pre-draw frames are fed in parallel at the same time. In the cotton feeding roller, the pre-drawn bars of the same color are concentratedly distributed on the cotton guide plate, and are made into four-color cooked slivers after the drawing process.
[0085] Next, on the traditional roving frame equipment, multi-color auxiliary-color rovings are spun. The roving ration is 5.2 g / 10 meters, and the roving twist is 51 twists / meter.
[0086]...
PUM
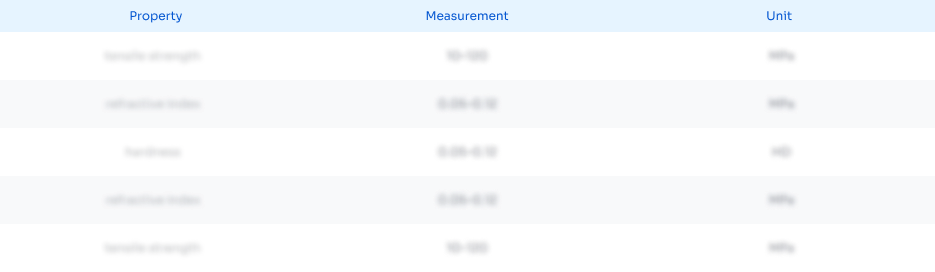
Abstract
Description
Claims
Application Information

- R&D Engineer
- R&D Manager
- IP Professional
- Industry Leading Data Capabilities
- Powerful AI technology
- Patent DNA Extraction
Browse by: Latest US Patents, China's latest patents, Technical Efficacy Thesaurus, Application Domain, Technology Topic, Popular Technical Reports.
© 2024 PatSnap. All rights reserved.Legal|Privacy policy|Modern Slavery Act Transparency Statement|Sitemap|About US| Contact US: help@patsnap.com