A large thickness blunt trailing edge wind turbine blade
A blunt trailing edge and large-thickness technology is applied in the field of wind turbine blades and large-thickness blunt trailing edge wind turbine blades to achieve the effects of improving aerodynamic performance, improving structural efficiency and reducing blade mass.
- Summary
- Abstract
- Description
- Claims
- Application Information
AI Technical Summary
Problems solved by technology
Method used
Image
Examples
Embodiment Construction
[0034] In order to make the object, technical solution and advantages of the present invention clearer, the present invention will be further described in detail below with reference to the accompanying drawings and examples.
[0035] refer to figure 1, the large-thickness blunt trailing edge wind turbine blade of the present invention includes a blade cylindrical section 10, a blade transition section 20 and a blade front end 30, and the blade transition section between the circular section 1 connecting the blade root and the maximum chord length section 2 of the blade Within 20, select one or more spanwise positions to place one or more standard airfoil families with large thickness blunt trailing edges developed by the Institute of Engineering Thermophysics, Chinese Academy of Sciences, with a relative thickness of more than 40%, see Figures 2 to 6 , the relative thickness of the airfoil includes four types of large-thickness blunt trailing edge airfoils of 45%, 50%, 55% ...
PUM
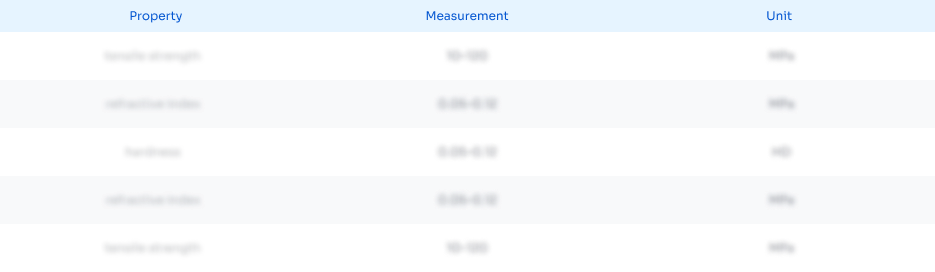
Abstract
Description
Claims
Application Information

- R&D
- Intellectual Property
- Life Sciences
- Materials
- Tech Scout
- Unparalleled Data Quality
- Higher Quality Content
- 60% Fewer Hallucinations
Browse by: Latest US Patents, China's latest patents, Technical Efficacy Thesaurus, Application Domain, Technology Topic, Popular Technical Reports.
© 2025 PatSnap. All rights reserved.Legal|Privacy policy|Modern Slavery Act Transparency Statement|Sitemap|About US| Contact US: help@patsnap.com