Method for producing a yankee cylinder
A cylinder shell and place technology, applied in the direction of manufacturing tools, paper making, paper machines, etc., can solve the problems of consuming too much effort and cost, and no way to transport parts to customers
- Summary
- Abstract
- Description
- Claims
- Application Information
AI Technical Summary
Problems solved by technology
Method used
Image
Examples
Embodiment Construction
[0047] figure 1 A Yankee cylinder 1 is shown. The Yankee cylinder 1 comprises a cylindrical steel casing 2 which is welded or bolted to two end covers 3 and 4 .
[0048] Inside the Yankee cylinder 1 there is a central shaft 7 with a central part 21 and two bearing shafts 20 which rotate in bearings 17 .
[0049] During operation, steam is supplied to the Yankee cylinder 1 via a steam feed 18 . Waste steam and condensate exit the Yankee via condensate lines 22 and 19, respectively.
[0050] On the cylinder interior 15 there are a large number of grooves 11 which extend in the circumferential direction of the Yankee cylinder 1 . Through the grooves 11, the transfer of heat to the cylinder exterior 16 is enhanced and the removal of condensed water is facilitated.
[0051] In the manufacturing methods used so far in the prior art, individual shell plates are cut, crimped and welded together to form cylinder sections. Afterwards, the entire cylinder housing is machined on the ...
PUM
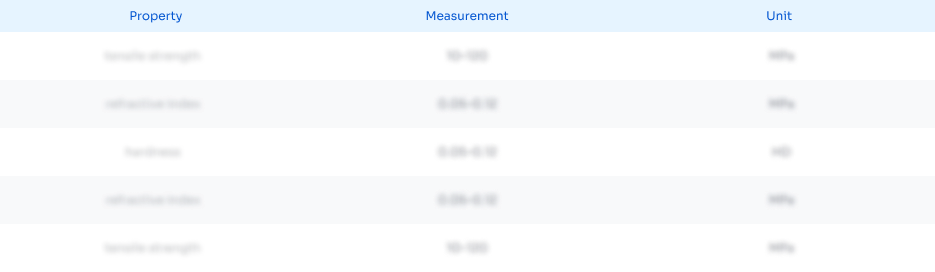
Abstract
Description
Claims
Application Information

- R&D
- Intellectual Property
- Life Sciences
- Materials
- Tech Scout
- Unparalleled Data Quality
- Higher Quality Content
- 60% Fewer Hallucinations
Browse by: Latest US Patents, China's latest patents, Technical Efficacy Thesaurus, Application Domain, Technology Topic, Popular Technical Reports.
© 2025 PatSnap. All rights reserved.Legal|Privacy policy|Modern Slavery Act Transparency Statement|Sitemap|About US| Contact US: help@patsnap.com