Self moving ground-handling robot and cleaning control method thereof
A control method and robot technology, applied in the field of intelligent robots, can solve problems such as incomplete cleaning work, affecting cleaning efficiency, and inability to clean the edge area of obstacles
- Summary
- Abstract
- Description
- Claims
- Application Information
AI Technical Summary
Problems solved by technology
Method used
Image
Examples
Embodiment 1
[0043] like figure 1 It is a structural block diagram of the self-moving ground handling robot of the present invention, which includes a cleaning unit 1, a walking unit 2, a driving unit 3, an obstacle sensor 4 and a control unit 5 at the front end of the robot. like figure 2 As shown, the self-propelled ground handling robot is a cleaning robot, and the cleaning robot includes a body 6 , and a strike plate 61 is provided at the front of the body 6 , and the obstacle sensor 4 is arranged on the strike plate 61 . Robots generally use obstacle sensors to detect surrounding obstacles to avoid or stick to the side. Specifically, the obstacle sensor may be an ultrasonic sensor, an infrared sensor, a travel switch, and the like. For example, when the ultrasonic sensor is working, it transmits the ultrasonic signal to the path of the robot, and receives the ultrasonic signal reflected from the obstacle, so as to determine whether the obstacle exists and the distance from the obst...
Embodiment 2
[0052] like Figure 5-6 As shown, the present invention provides another control method for the small-area cleaning work of the self-moving ground handling robot.
[0053] After the same power is turned on, the robot starts to walk randomly in the room (step S0), and continues to walk randomly after the robot collides with obstacles (step S1). ), the control unit determines that it has entered a small area, and starts the small area cleaning mode.
[0054] After this mode is activated, the robot starts to perform small area cleaning work, assuming that it is still cleaning according to the bow-shaped path. The robot first cleans towards one side (step S21'). When it is judged that the distance of the straight line section of the bow-shaped walk is within the range of 30-180 cm, the control unit controls the robot to continue walking; when it is judged that the distance of the straight line section of walking is not within the range ( Step S25), the control unit controls the ...
PUM
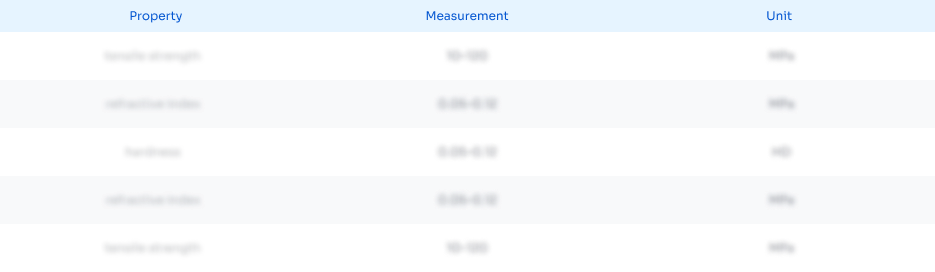
Abstract
Description
Claims
Application Information

- R&D
- Intellectual Property
- Life Sciences
- Materials
- Tech Scout
- Unparalleled Data Quality
- Higher Quality Content
- 60% Fewer Hallucinations
Browse by: Latest US Patents, China's latest patents, Technical Efficacy Thesaurus, Application Domain, Technology Topic, Popular Technical Reports.
© 2025 PatSnap. All rights reserved.Legal|Privacy policy|Modern Slavery Act Transparency Statement|Sitemap|About US| Contact US: help@patsnap.com