Split elbow mold
A split-type elbow technology, applied in the field of split-type elbow molds, can solve the problems of time-consuming and labor-intensive demoulding, and achieve the effect of light weight, easy handling and assembly, and easy demoulding
- Summary
- Abstract
- Description
- Claims
- Application Information
AI Technical Summary
Problems solved by technology
Method used
Image
Examples
Embodiment Construction
[0015] The present invention will be further described below in conjunction with the accompanying drawings.
[0016] Such as figure 1 , figure 2 As shown, the traditional FRP elbow mold is an expansive overall structure, including the elbow mold body 1 and the rotating support rod 2. There is an arc seam b=10~20mm wide on the inner arc surface of the elbow mold body 1. Stuff the expansion strips between the seams 3.
[0017] When demolding, first take off the expansion strip 3 in the arc seam, make the mold shrink, and then take off the product.
[0018] Due to the large contact surface between the mold and the product, it is often difficult to demould.
[0019] When the two ends are sockets with larger diameters, the mold of the overall structure cannot be demoulded, and it needs to be molded separately before hand lay-up butt joint.
[0020] Such as image 3 As shown, the present invention includes an elbow mold body 1, a rotating support rod 2, and two pieces of mold ...
PUM
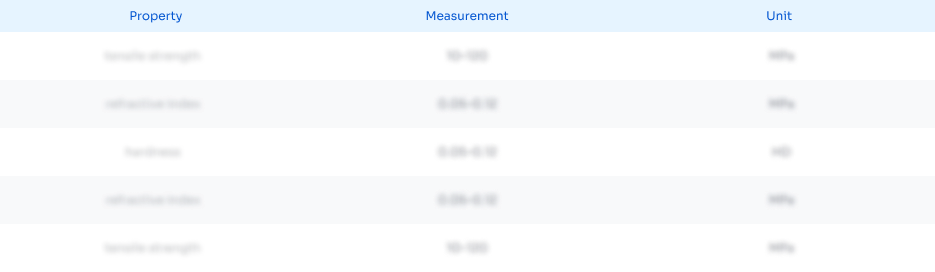
Abstract
Description
Claims
Application Information

- R&D
- Intellectual Property
- Life Sciences
- Materials
- Tech Scout
- Unparalleled Data Quality
- Higher Quality Content
- 60% Fewer Hallucinations
Browse by: Latest US Patents, China's latest patents, Technical Efficacy Thesaurus, Application Domain, Technology Topic, Popular Technical Reports.
© 2025 PatSnap. All rights reserved.Legal|Privacy policy|Modern Slavery Act Transparency Statement|Sitemap|About US| Contact US: help@patsnap.com