Parameter compensation method and control method for short stroke control of head-tail width of strip steel
A technology of short-stroke control and parameter compensation, which is applied in the direction of metal rolling stands and metal rolling mill stands, and can solve the problems of affecting product width accuracy and reducing the width adjustment efficiency of vertical roll rolling, etc.
- Summary
- Abstract
- Description
- Claims
- Application Information
AI Technical Summary
Problems solved by technology
Method used
Image
Examples
Embodiment 1
[0140] Embodiment 1 Silicon steel width control method
[0141] In this embodiment, the head and tail width of a batch of steel whose steel type is DW60 is controlled by the following method, and the head and tail width of the slab is controlled,
[0142] (1) Control the width of the finished slab by file
[0143] Wherein according to the measured width of the slab measured by the slab width measuring instrument device, according to the method calculation of the specific embodiment of the invention table 2 and 3, the blank width for control and the target width of the finished product are calculated, specifically as shown in the following table:
[0144] The blank and the width data of finished product in the embodiment 1 of table 7
[0145] Blank measured width (mm)
Blank Width for Control (mm)
Finished product target width (mm)
1253.646
1255
1255
1262.936
1265
1268
1255.825
1255
1255
1243.29
1245
124...
Embodiment 2
[0152] Embodiment 2: stainless steel width control method
[0153] 1. Control the width of the finished slab by file
[0154] 1.1 Use the calculation method in Table 4-6 to control the head and tail width of a batch of 430 steel. Wherein, according to the measured width of the slab measured by the slab width measuring instrument device, the actual measured width of the slab determined according to the calculation method in Table 4-6 of the specific embodiment of the invention, the blank width for control, the nominal width of the finished product, and the finished product width data for control are as follows As shown in the table:
[0155] Table 9 The width data of blanks and finished products of steel grade 430
[0156]
[0157] 1.2 Control the head and tail width of a batch of steel with steel type 409 through the calculation method in Table 4-6. Wherein, according to the actual measured width of the slab measured by the slab width measuring instrument device, the act...
Embodiment 3
[0172] Embodiment 3: the width control method when the stainless steel blank width is too wide
[0173] 1. Control the width of the finished slab by file
[0174] Control the head-to-tail width of a batch of 430 steel by the calculation method in Table 4-6. Wherein, according to the measured width of the slab measured by the slab width measuring instrument device, the actual measured width of the slab determined according to the calculation method in Table 4-6 of the specific embodiment of the invention, the blank width for control, the nominal width of the finished product, and the finished product width data for control are as follows As shown in the table:
[0175] Table 14: Width data of blanks and finished products of steel grade 430
[0176] Billet measured width (mm)
Blank width for control (mm)
Finished nominal width (mm)
Finished product width for control (mm)
1290.354
1290
1235
1253
1288.141
1290
1235
1253 ...
PUM
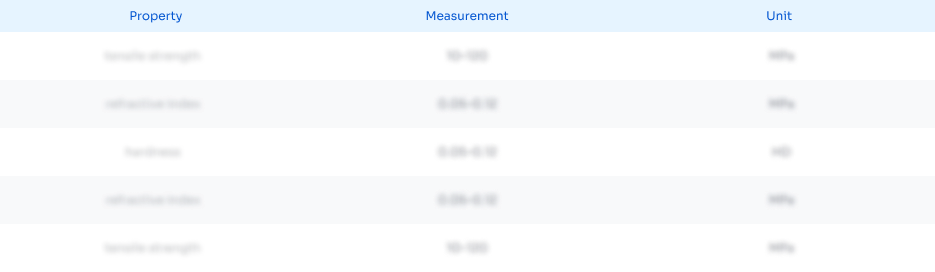
Abstract
Description
Claims
Application Information

- R&D Engineer
- R&D Manager
- IP Professional
- Industry Leading Data Capabilities
- Powerful AI technology
- Patent DNA Extraction
Browse by: Latest US Patents, China's latest patents, Technical Efficacy Thesaurus, Application Domain, Technology Topic, Popular Technical Reports.
© 2024 PatSnap. All rights reserved.Legal|Privacy policy|Modern Slavery Act Transparency Statement|Sitemap|About US| Contact US: help@patsnap.com