Automatic balancing magnetic suspension rotor system based on displacement stiffness force lead compensation
A magnetic levitation rotor and automatic balancing technology, which is applied in general control systems, control/regulation systems, torque/mechanical power control, etc., can solve problems such as lagging, reducing the effect of automatic balancing, and failing to meet the requirements of automatic balancing of magnetic levitating rotors.
- Summary
- Abstract
- Description
- Claims
- Application Information
AI Technical Summary
Problems solved by technology
Method used
Image
Examples
Embodiment Construction
[0023] Such as image 3 As shown, the automatic balancing magnetic levitation rotor system based on displacement stiffness force advanced compensation used in this embodiment includes an automatic balancing module 1, a stability controller 2, a magnetic bearing power amplifier 3, an electromagnet-rotor 4, and a displacement sensor 5. The displacement sensor 5 detects the position of the electromagnet-rotor 4 in real time, and converts the rotor displacement into a voltage signal output; the automatic balance module 1 receives the rotor displacement signal output by the displacement sensor 5, implements an automatic balance control algorithm, and outputs non-same-frequency displacement signals and the same frequency compensation signal; the stability controller 2 receives the non-same-frequency displacement signal output by the automatic balance module 1, and runs the magnetic bearing stability control algorithm to generate a non-same-frequency control signal to stabilize the ro...
PUM
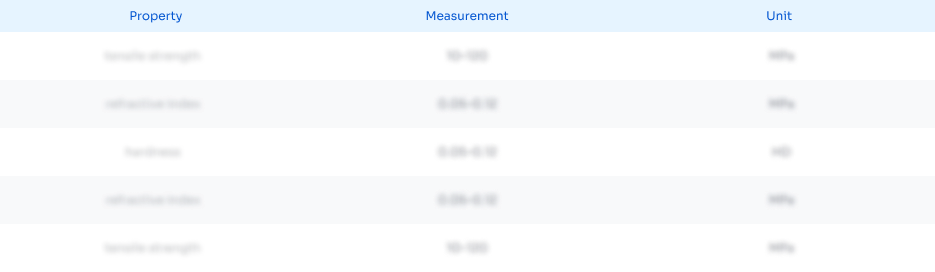
Abstract
Description
Claims
Application Information

- R&D
- Intellectual Property
- Life Sciences
- Materials
- Tech Scout
- Unparalleled Data Quality
- Higher Quality Content
- 60% Fewer Hallucinations
Browse by: Latest US Patents, China's latest patents, Technical Efficacy Thesaurus, Application Domain, Technology Topic, Popular Technical Reports.
© 2025 PatSnap. All rights reserved.Legal|Privacy policy|Modern Slavery Act Transparency Statement|Sitemap|About US| Contact US: help@patsnap.com