Failure prediction method based on ICA reconstruction
A technology of fault prediction and fault direction, which is applied in the testing of machines/structural components, measuring devices, and measuring ultrasonic/sonic/infrasonic waves, etc., can solve the problem of few results, reduce the rate of false alarms and missed alarms, and improve The effect of forecast accuracy
- Summary
- Abstract
- Description
- Claims
- Application Information
AI Technical Summary
Benefits of technology
Problems solved by technology
Method used
Image
Examples
Embodiment Construction
[0032] The fault prediction method provided by the invention is based on figure 1 To proceed, follow the steps below:
[0033] Step 1), using historical normal process data X to establish an independent meta-analysis model, which describes the relationship between different locations and different types of sensors;
[0034] Step 2), select the relatively stable historical fault data X that has occurred before fault , to extract the fault direction matrix Ξ.
[0035] Step 3), according to the real-time measurement sample of sensor, detect the fault that occurs in the process;
[0036] Step 4), use the known fault direction Ξ to identify the fault, and further estimate the magnitude of the fault.
[0037] Step 5), modeling and predicting the obtained fault amplitude using a support vector machine (SVM) and an autoregressive (AR) model.
[0038] Step 1) includes:
[0039] Step 10), standardize and whiten the historical normal data, and assume that the number of variables is ...
PUM
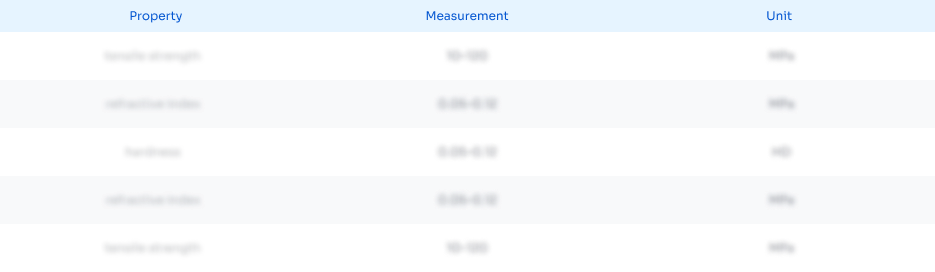
Abstract
Description
Claims
Application Information

- R&D Engineer
- R&D Manager
- IP Professional
- Industry Leading Data Capabilities
- Powerful AI technology
- Patent DNA Extraction
Browse by: Latest US Patents, China's latest patents, Technical Efficacy Thesaurus, Application Domain, Technology Topic, Popular Technical Reports.
© 2024 PatSnap. All rights reserved.Legal|Privacy policy|Modern Slavery Act Transparency Statement|Sitemap|About US| Contact US: help@patsnap.com