Processing method of coal and oil co-refining
A treatment method and co-smelting technology, which is applied in the upgrading field of coal and low-quality heavy oil co-smelting, can solve the problems of low conversion rate and easy clogging of solid coal powder, and achieve improved reaction effect, improved fusion effect, and improved degassing The effect of the ability to remove impurities
- Summary
- Abstract
- Description
- Claims
- Application Information
AI Technical Summary
Benefits of technology
Problems solved by technology
Method used
Image
Examples
Embodiment -1
[0021] The mixed raw material of Tahe residual oil and Ningxia lignite (the blending ratio of coal is 35% of the residual oil quality) and tetralin joins the static mixer, (keep excess tetralin, coal and oil co-refining raw material and The weight ratio of tetrahydronaphthalene is 1: 6), after the material is heated, enter CSTR (continuously stirred tank reactor), pressurize, heat up and start to stir, rotating speed 800 revs / min, pressurize to 20MPa, heat up to 400 ℃, The reaction time is 3h. The reacted product enters the separator after being filtered to separate the gas phase and the liquid phase, and the solid impurities separated by filtration can be burned or used as raw materials for the production of needle coke, and the liquid phase enters the fractionation tower. The fractionation column separates the various products as well as excess hydrogen-donating solvent. Excess hydrogen donating solvent can be recycled. The reaction effect is shown in Table 1.
Embodiment -2
[0023] Using the mixture of Tahe residual oil and Ningxia lignite as raw material (the blending ratio of coal is 5% of the residual oil quality), the steps are the same as in Example-1, the hydrogen-donating solvent is decahydronaphthalene, and the coal and oil co-refining raw material and The hydrogen-donating solvent weight ratio is 1: 2, the reaction pressure is 35MPa, the reaction temperature is 450°C, and the reaction time is 0.5h (CSTR is continuous feeding and discharging, and the reaction time is the average residence time of the material), after being processed by the method of the present invention After that, the reaction results are shown in Table 2.
Embodiment -3
[0025] By the same method as in Example 2, water was added simultaneously, and the weight ratio of water to coal and oil co-refining raw materials was 1: 1. The reaction results are shown in Table 2.
PUM
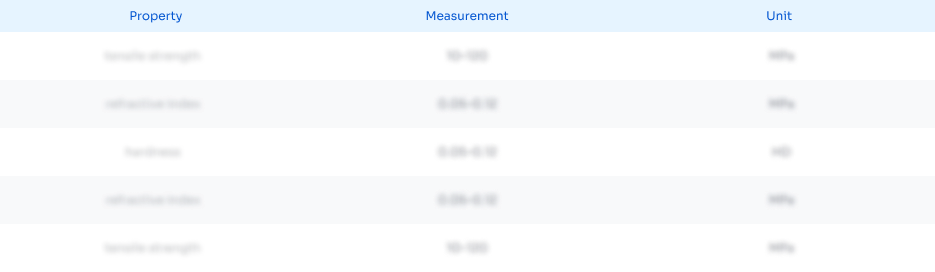
Abstract
Description
Claims
Application Information

- R&D Engineer
- R&D Manager
- IP Professional
- Industry Leading Data Capabilities
- Powerful AI technology
- Patent DNA Extraction
Browse by: Latest US Patents, China's latest patents, Technical Efficacy Thesaurus, Application Domain, Technology Topic, Popular Technical Reports.
© 2024 PatSnap. All rights reserved.Legal|Privacy policy|Modern Slavery Act Transparency Statement|Sitemap|About US| Contact US: help@patsnap.com