Robot calibration method based on exponent product model
A calibration method and robot technology, applied in the field of robot calibration, to achieve the effect of small introduction error, avoidance of conversion and good stability
- Summary
- Abstract
- Description
- Claims
- Application Information
AI Technical Summary
Problems solved by technology
Method used
Image
Examples
Embodiment Construction
[0024] see figure 1 , a robot calibration method based on an exponential product model, which provides a robot 1 for industrial use, a measuring instrument 3 independent of the robot, a terminal stereo imaging device 2 and a stereo calibration block 4 . The terminal stereoscopic imaging equipment is installed at the end of the robot in a detachable connection mode, the measuring instrument is installed on the ground support at the calibration site, and the stereoscopic calibration block is located at the position where both the measuring instrument and the terminal stereoscopic imaging equipment can be detected at the calibration site.
[0025] combine figure 2 , {W} indicates the world coordinate system, which is established on the measuring instrument, and {T} indicates that the tool coordinate system is established on the terminal stereoscopic imaging device. The purpose of robot positioning is to determine the coordinates of the space point P in the world coordinate syst...
PUM
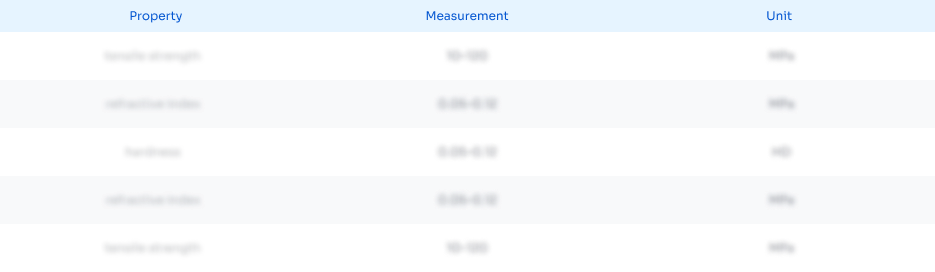
Abstract
Description
Claims
Application Information

- Generate Ideas
- Intellectual Property
- Life Sciences
- Materials
- Tech Scout
- Unparalleled Data Quality
- Higher Quality Content
- 60% Fewer Hallucinations
Browse by: Latest US Patents, China's latest patents, Technical Efficacy Thesaurus, Application Domain, Technology Topic, Popular Technical Reports.
© 2025 PatSnap. All rights reserved.Legal|Privacy policy|Modern Slavery Act Transparency Statement|Sitemap|About US| Contact US: help@patsnap.com