Process for combined continuous casting of double sections
A continuous casting process and cross-section technology, which is applied in the field of double-section combined continuous casting technology, can solve problems such as the inability to realize hot delivery and hot charging of billets, restricting the production capacity of rolled products, and stopping and waiting for materials, so as to improve capital turnover and reduce production. Time and energy saving effects
- Summary
- Abstract
- Description
- Claims
- Application Information
AI Technical Summary
Problems solved by technology
Method used
Image
Examples
Embodiment Construction
[0025] Embodiment: six-machine six-strand billet continuous casting machine, the production section is 180mm×180mm, 240mm×240mm, and the steel output of the converter is 120 tons / furnace. The corresponding rolling production lines are as follows: large steel rolling production line, rolling specifications φ75mm~φ150mm, using 240mm×240mm billets, production capacity 1400~1800t / day; medium-sized production line, rolling specifications φ45mm~φ75mm, using 180mm×180mm billets, production capacity 800~1000t / day; small-scale production line, rolling specification φ25mm~φ50mm, using 180mm×180mm billet, production capacity 800~1000t / day. The daily output of the continuous casting machine is 3,600-4,200 tons, and each section is continuously produced for 3-5 days. With a single section, any production line cannot digest the billets produced in time, and cannot realize hot delivery and hot charging of the billets, resulting in a great waste of energy; At the same time, a large area is re...
PUM
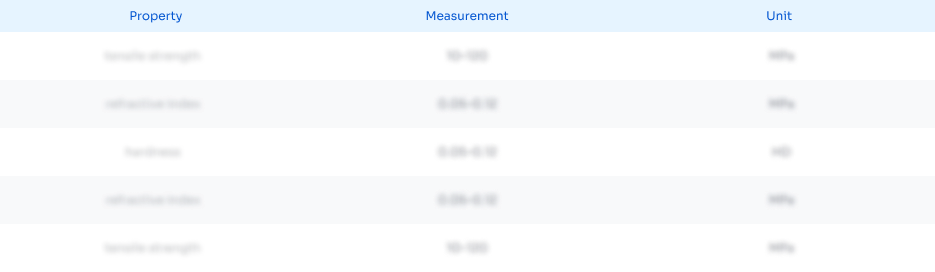
Abstract
Description
Claims
Application Information

- R&D
- Intellectual Property
- Life Sciences
- Materials
- Tech Scout
- Unparalleled Data Quality
- Higher Quality Content
- 60% Fewer Hallucinations
Browse by: Latest US Patents, China's latest patents, Technical Efficacy Thesaurus, Application Domain, Technology Topic, Popular Technical Reports.
© 2025 PatSnap. All rights reserved.Legal|Privacy policy|Modern Slavery Act Transparency Statement|Sitemap|About US| Contact US: help@patsnap.com