Parallel crank guide rod self-rotating positioning mechanical arm
A manipulator and guide rod technology, applied in the field of manipulators, can solve the problems of low positioning accuracy, complicated mechanism, slow movement, etc., and achieve the effects of low positioning dependence, simple structure and reliable clamping.
- Summary
- Abstract
- Description
- Claims
- Application Information
AI Technical Summary
Problems solved by technology
Method used
Image
Examples
Embodiment Construction
[0019] The present invention is described in more detail below in conjunction with accompanying drawing example:
[0020] Referring to Fig. 1, the parallel crank guide rod self-rotation positioning manipulator is composed of four parts: the interface frame, the drive positioning, the parallel crank guide rod clamping mechanism and the self-rotation positioning finger; the interface frame includes a fixed plate 13 and a manipulator installed on the fixed plate The interface mechanism 8; the drive positioning part includes a motor 11 installed on the fixed disk, a motor code disc 10 installed at the rear of the motor and a travel switch 5 installed on the end of the guide rod 6; the parallel guide rod clamping mechanism includes the guide rod 6 , the rotation moving pair 7, the crank turning pair 9 and the crank disc 12 connected on the motor output shaft, the guide rod 6 is hinged with the crank disc 12 through the crank turning pair 9, and the rotation moving pair 7 is arranged...
PUM
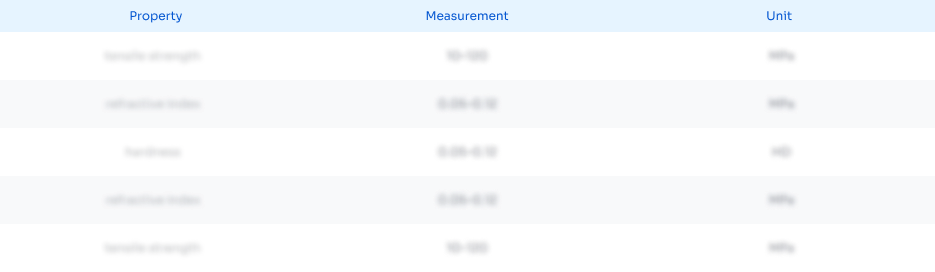
Abstract
Description
Claims
Application Information

- Generate Ideas
- Intellectual Property
- Life Sciences
- Materials
- Tech Scout
- Unparalleled Data Quality
- Higher Quality Content
- 60% Fewer Hallucinations
Browse by: Latest US Patents, China's latest patents, Technical Efficacy Thesaurus, Application Domain, Technology Topic, Popular Technical Reports.
© 2025 PatSnap. All rights reserved.Legal|Privacy policy|Modern Slavery Act Transparency Statement|Sitemap|About US| Contact US: help@patsnap.com