Vibration mirror motor
A galvanometer motor and rotor technology, applied in electric components, electrical components, electromechanical devices, etc., can solve the problems of limited response speed, low axial stiffness, affecting running accuracy, etc., to achieve positioning, eliminate drift, and improve performance. Effect
- Summary
- Abstract
- Description
- Claims
- Application Information
AI Technical Summary
Problems solved by technology
Method used
Image
Examples
Embodiment Construction
[0023] Such as Figure 1-Figure 6 As shown, the vibrating mirror motor 1 of the present invention includes a fixed stator 2 and a rotor 3 that rotates relative to the stator 2 . Among them, the stator 2 includes a coil 5, a skeleton 6 and a yoke 7. The skeleton 6 is made of a non-magnetic material, and long slots are arranged on it at intervals. For the multi-pole winding, the coil 5 and the skeleton 6 are vacuum-cast in the yoke 7 by epoxy resin. The rotor 3 includes a magnet 8, a rotating shaft 9 and a bearing 10. A plurality of magnets 8 with alternating polarities are pasted on the magnetic rotating shaft 9 to form a multi-pole rotor. The magnetic rotating shaft 9 includes a main shaft (not shown) covered by the magnet 8, which is High magnetic permeability material, the two ends are respectively connected to non-magnetic shaft extensions 11 and 12, the bearing 10 is an angular contact ball bearing, installed on the non-magnetic shaft extensions 11 and 12, and the compres...
PUM
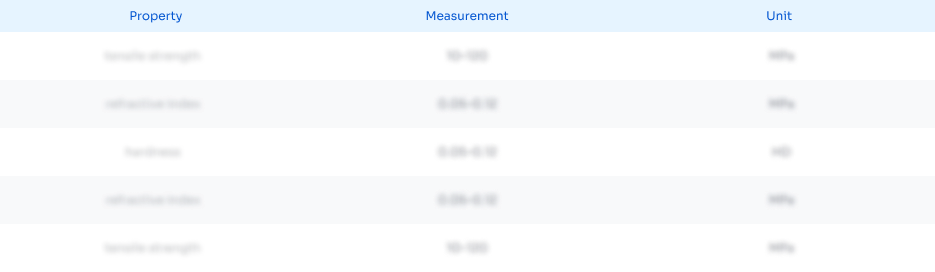
Abstract
Description
Claims
Application Information

- R&D
- Intellectual Property
- Life Sciences
- Materials
- Tech Scout
- Unparalleled Data Quality
- Higher Quality Content
- 60% Fewer Hallucinations
Browse by: Latest US Patents, China's latest patents, Technical Efficacy Thesaurus, Application Domain, Technology Topic, Popular Technical Reports.
© 2025 PatSnap. All rights reserved.Legal|Privacy policy|Modern Slavery Act Transparency Statement|Sitemap|About US| Contact US: help@patsnap.com