Position sensor which is intended, in particular, for measuring steering column torsion
A sensor and steering column technology, applied in the field of sensors, can solve problems such as the use of expensive components and low sensitivity of sensors
- Summary
- Abstract
- Description
- Claims
- Application Information
AI Technical Summary
Problems solved by technology
Method used
Image
Examples
Embodiment Construction
[0083] 1 and 2 are views showing a third magnetic structure of the sensor. The fixed collector structure 30 collects the magnetic flux (magnetic flux) on the stator rings 23 , 24 and concentrates it in the measuring gap 40 .
[0084] The structure comprises two parts 31 , 32 formed respectively by disk-shaped arc segments 33 , 34 configured such that a magnetic flux transmission occurs between the stator and the collecting poles in the axial direction of the sensor.
[0085] The collectors 31 , 32 have arc segments 33 , 34 whose radial width is smaller than the radial width of the stator rings 23 , 24 and which make it possible to tolerate eccentricity defects between the stator structure 20 and the collector structure 30 .
[0086] The collector parts 31 , 32 have a greater offset between the disk-shaped segments 33 , 34 and the surfaces 37 , 38 forming the measuring gap 40 .
[0087] This particular structure makes it possible to limit flux leakage between the collector por...
PUM
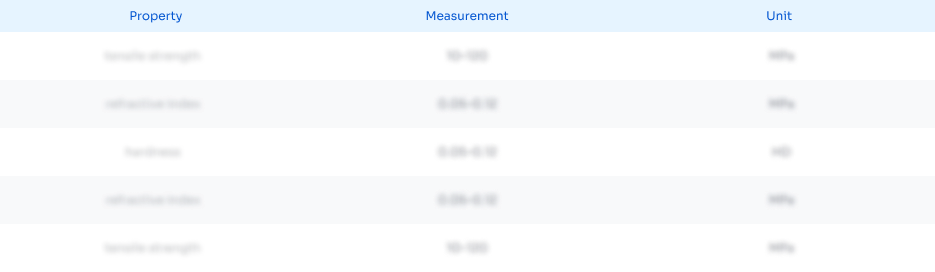
Abstract
Description
Claims
Application Information

- R&D
- Intellectual Property
- Life Sciences
- Materials
- Tech Scout
- Unparalleled Data Quality
- Higher Quality Content
- 60% Fewer Hallucinations
Browse by: Latest US Patents, China's latest patents, Technical Efficacy Thesaurus, Application Domain, Technology Topic, Popular Technical Reports.
© 2025 PatSnap. All rights reserved.Legal|Privacy policy|Modern Slavery Act Transparency Statement|Sitemap|About US| Contact US: help@patsnap.com