Component model order reduction method facing products grade simulated components
A technology of model reduction and components, which is applied in the field of computer-aided collaborative product simulation, can solve the problems of large number of components and high difficulty, and achieve the effect of improving reusability, increasing simulation speed, and shortening product development cycle
- Summary
- Abstract
- Description
- Claims
- Application Information
AI Technical Summary
Problems solved by technology
Method used
Image
Examples
Embodiment Construction
[0028] The simulation method is a model reduction method for component structures, which includes the following three modules, such as figure 1 As shown, they are:
[0029] 1. Component Modeling Module
[0030] This module is mainly to establish the 3D mesh model of the parts, and provide the basic model for other modules to complete detailed simulation, order reduction and other calculations. The steps involved are as follows:
[0031] Step 1.1 establishes the three-dimensional solid model of the component. According to the actual size and material of the parts, through input devices such as mouse and keyboard, use ANSYS software to manually build its model, and the established 3D model is saved in model.sat format.
[0032] Step 1.2 meshes the component model. In ANSYS software, for the 3D solid modeling of parts established in step 1.1, the 3D model is divided into tetrahedral meshes by mouse, keyboard and other input devices in the order from line to surface and from su...
PUM
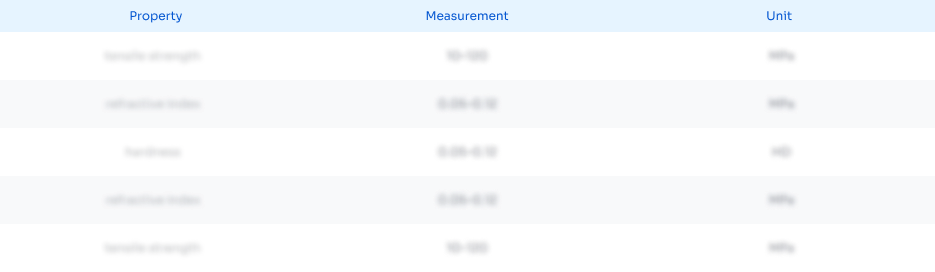
Abstract
Description
Claims
Application Information

- R&D
- Intellectual Property
- Life Sciences
- Materials
- Tech Scout
- Unparalleled Data Quality
- Higher Quality Content
- 60% Fewer Hallucinations
Browse by: Latest US Patents, China's latest patents, Technical Efficacy Thesaurus, Application Domain, Technology Topic, Popular Technical Reports.
© 2025 PatSnap. All rights reserved.Legal|Privacy policy|Modern Slavery Act Transparency Statement|Sitemap|About US| Contact US: help@patsnap.com