Stepping type feeding mechanism capable of adjusting feeding distance
A technology of feeding distance and feeding mechanism, which is applied in the field of step-by-step feeding mechanism, can solve the problems of large force on the rocker, the equipment is not widely used, and cannot change speed, and achieves the effect of avoiding the fragile structure
- Summary
- Abstract
- Description
- Claims
- Application Information
AI Technical Summary
Problems solved by technology
Method used
Image
Examples
Embodiment Construction
[0025] In order to enable those skilled in the art to better understand the technical solutions of the present invention, the present invention will be described more clearly and completely below in conjunction with the accompanying drawings in the embodiments. Of course, the described embodiments are only a part of the present invention. Not all, based on this embodiment, other embodiments obtained by those skilled in the art without creative efforts are all within the protection scope of the present invention.
[0026] Such as Figure 1 to Figure 6 As shown, a step-by-step feeding mechanism that can adjust the feeding distance includes a platform 11 for transporting the material 4 and two transport claws 12 arranged on both sides of the platform 11. Conical cam power part, the conical cam power part rotates and pushes the transportation claw 12 to make oblique reciprocating motion along the side of the platform 11. The conical cam power part is provided with two conical cams...
PUM
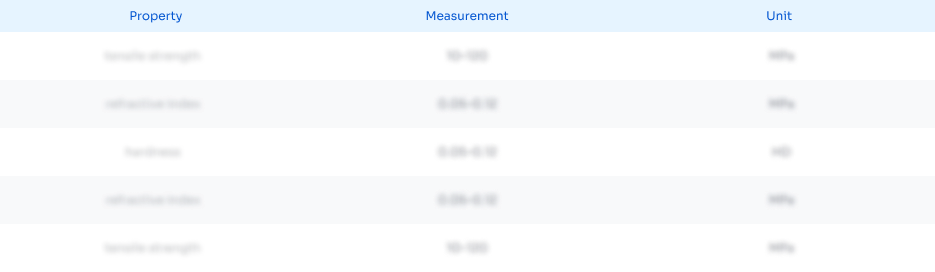
Abstract
Description
Claims
Application Information

- Generate Ideas
- Intellectual Property
- Life Sciences
- Materials
- Tech Scout
- Unparalleled Data Quality
- Higher Quality Content
- 60% Fewer Hallucinations
Browse by: Latest US Patents, China's latest patents, Technical Efficacy Thesaurus, Application Domain, Technology Topic, Popular Technical Reports.
© 2025 PatSnap. All rights reserved.Legal|Privacy policy|Modern Slavery Act Transparency Statement|Sitemap|About US| Contact US: help@patsnap.com