Preparation method of La modified Cu-SSZ-13 molecular sieve
A cu-ssz-13, molecular sieve technology, applied in separation methods, molecular sieve catalysts, molecular sieves and alkali exchange compounds, etc., can solve the problems of low NO conversion rate, excessive NO conversion rate drop, etc., and achieve good N2 selectivity. Effect
- Summary
- Abstract
- Description
- Claims
- Application Information
AI Technical Summary
Benefits of technology
Problems solved by technology
Method used
Image
Examples
Embodiment 1
[0026] 1. Experimental steps
[0027] Silica sol (40%), copper sulfate, tetraethylenepentamine (TEPA), sodium metaaluminate and sodium hydroxide are used as silicon source, copper source, template agent, aluminum source and alkaline regulator respectively. Weigh 22-23gCuSO 4 ·5H 2 O add 113-114gH 2 O dissolves and completely dissolves into a dark blue transparent liquid. Add 7-8g NaAlO 2 After stirring for 0.5 hours, it turned into a sky blue mud. Then add 20-21g TEPA to turn dark blue, stir well. Continue to add 14-15g NaOH and stir for 0.5h, then add 67-68g of 40.06% silica sol, stir for 2h to obtain the initial aluminosilicate gel, the molar ratio of the prepared initial aluminosilicate gel is 5.0Na 2 O:1.0Al 2 o 3 :10SiO2 2 :200H 2 O: 2.0Cu-TEPA, put the aluminosilicate initial gel into the reaction kettle for crystallization at 140°C for 3 days. The crystallized product was washed with deionized water until the pH was neutral, and dried at 110°C for 8 hours to ...
Embodiment 2
[0033] 1. Experimental steps
[0034] Prepared Cu-SSZ-13, La in embodiment 1 0.015 -Cu-SSZ-13, La 0.025 -Cu-SSZ-13, La 0.10 -Cu-SSZ-13, La0.15-Cu-SSZ-13 respectively in the range of 150 ℃ -550 ℃, the space velocity is set to 150,000h-1 test conditions, La modified Cu-SSZ-13 and Cu - The "standard SCR" denitrification activity of SSZ-13 catalyst was investigated.
[0035] NH 3 Selective catalytic reduction of NO experiments were carried out in a miniature fixed-bed quartz reactor (i.d.=5 mm). The loading amount of the catalyst (20-40 mesh) is 80 mg, and the reaction pressure is 0.1 MPa. Intake composition is 500ppm NO, 500ppm NH 3 , 5.0%O 2 , and the balance gas nitrogen. The total gas flow rate is 100mL / min, which corresponds to a GHSV of 150000h-1. The NO gas at the outlet of the reactor was analyzed online with the KM.9106 integrated flue gas analyzer of KANE, UK. Data recording was carried out when the steady state was reached after 30 min of reaction.
[0036] 2...
Embodiment 3
[0040] 1. Experimental steps
[0041] Weigh 22-23gCuSO 4 ·5H 2 O add 113-114gH 2 O dissolves and completely dissolves into a dark blue transparent liquid. Add 7-8g NaAlO 2 After stirring for 0.5 hours, it turned into a sky blue mud. Then add 20-21g TEPA to turn dark blue, stir well. Continue to add 14-15g NaOH and stir for 0.5h, then add 67-68g of 40.06% silica sol, stir for 2h to obtain the initial aluminosilicate gel, the molar ratio of the prepared initial aluminosilicate gel is 5.0Na 2 O:1.0Al 2 o 3 :10SiO2 2 :200H 2 O: 2.0Cu-TEPA, put the aluminosilicate initial gel into the reaction kettle for crystallization at 140°C for 3 days. The crystallized product was washed with deionized water until the pH was neutral, and dried at 110°C for 8 hours to obtain an initial Cu-SSZ-13 molecular sieve sample. The prepared initial Cu-SSZ-13 molecular sieve samples were treated with 1mol / L NH 4 NO 3 Perform ion exchange for 6h (according to 1g Cu-SSZ-13 molecular sieve with...
PUM
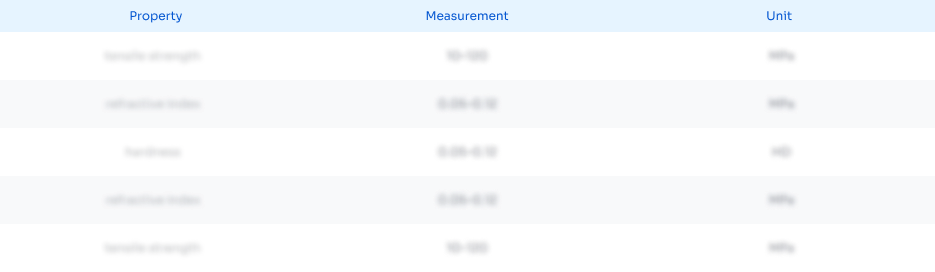
Abstract
Description
Claims
Application Information

- R&D
- Intellectual Property
- Life Sciences
- Materials
- Tech Scout
- Unparalleled Data Quality
- Higher Quality Content
- 60% Fewer Hallucinations
Browse by: Latest US Patents, China's latest patents, Technical Efficacy Thesaurus, Application Domain, Technology Topic, Popular Technical Reports.
© 2025 PatSnap. All rights reserved.Legal|Privacy policy|Modern Slavery Act Transparency Statement|Sitemap|About US| Contact US: help@patsnap.com