Inner cylinder surface defect detection method
A defect detection and inner cylinder technology, applied in the field of parts inspection, can solve the problems of cumbersome process and low part defect detection rate, and achieve the effect of improving speed, simplifying mechanical structure and inspection process, and improving accuracy and integrity.
- Summary
- Abstract
- Description
- Claims
- Application Information
AI Technical Summary
Problems solved by technology
Method used
Image
Examples
Embodiment 1
[0034] A method for detecting surface defects of an inner cylinder, comprising: a traditional turntable 1 and an improved conveyor belt 4, the center of the top of the traditional turntable 1 clamps a traditional inner cylindrical surface 2 to be inspected, and the traditional inner cylindrical surface to be inspected The right side of the top of the cylindrical surface 2 is bolted with a traditional single industrial camera 3, and the top of the improved conveyor belt 4 holds the improved inner cylindrical surface 5 to be inspected sequentially from left to right, and the improved inner cylindrical surface to be inspected The top of the surface 5 is bolted with a plurality of improved industrial cameras 6 sequentially from left to right;
[0035] The operation steps are as follows:
[0036] A. The improved inner cylindrical surface 5 to be detected is slowly and orderly driven on the improved conveyor belt 4, and then the improved industrial camera 6 is used to collect images...
Embodiment 2
[0042] In embodiment one, add following steps again:
[0043] The number of the improved industrial cameras 6 is at least three, and the improved industrial cameras 6 are symmetrically distributed along the center of the improved conveyor belt 4 .
[0044]A method for detecting surface defects of an inner cylinder, comprising: a traditional turntable 1 and an improved conveyor belt 4, the center of the top of the traditional turntable 1 clamps a traditional inner cylindrical surface 2 to be inspected, and the traditional inner cylindrical surface to be inspected The right side of the top of the cylindrical surface 2 is bolted with a traditional single industrial camera 3, and the top of the improved conveyor belt 4 holds the improved inner cylindrical surface 5 to be inspected sequentially from left to right, and the improved inner cylindrical surface to be inspected The top of the surface 5 is bolted with a plurality of improved industrial cameras 6 sequentially from left to ...
Embodiment 3
[0052] In embodiment two, add following steps again:
[0053] The improved industrial camera 6 collects image data for a single time, and the area of the image taken by the improved industrial camera 6 is larger than one-third of the inner surface of the improved inner cylindrical surface 5 to be inspected.
[0054] A method for detecting surface defects of an inner cylinder, comprising: a traditional turntable 1 and an improved conveyor belt 4, the center of the top of the traditional turntable 1 clamps a traditional inner cylindrical surface 2 to be inspected, and the traditional inner cylindrical surface to be inspected The right side of the top of the cylindrical surface 2 is bolted with a traditional single industrial camera 3, and the top of the improved conveyor belt 4 holds the improved inner cylindrical surface 5 to be inspected sequentially from left to right, and the improved inner cylindrical surface to be inspected The top of the surface 5 is bolted with a plura...
PUM
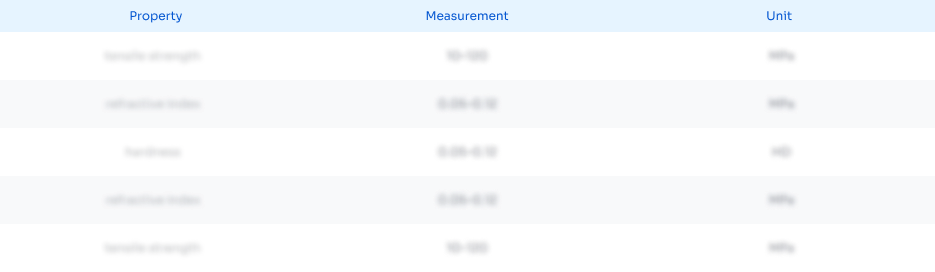
Abstract
Description
Claims
Application Information

- R&D Engineer
- R&D Manager
- IP Professional
- Industry Leading Data Capabilities
- Powerful AI technology
- Patent DNA Extraction
Browse by: Latest US Patents, China's latest patents, Technical Efficacy Thesaurus, Application Domain, Technology Topic, Popular Technical Reports.
© 2024 PatSnap. All rights reserved.Legal|Privacy policy|Modern Slavery Act Transparency Statement|Sitemap|About US| Contact US: help@patsnap.com