A debugging method for a six-degree-of-freedom displacement compensation platform
A technology of displacement change and debugging method, applied in the direction of electrical testing/monitoring, etc., can solve the problems affecting the performance of multi-degree-of-freedom platforms, long debugging cycle, and difficult debugging.
- Summary
- Abstract
- Description
- Claims
- Application Information
AI Technical Summary
Problems solved by technology
Method used
Image
Examples
Embodiment Construction
[0054] The technical solutions of the present invention will be further described below in conjunction with the accompanying drawings and through specific implementation methods.
[0055] The debugging method of the six-degree-of-freedom displacement compensation platform of this embodiment, such as figure 2 As shown, the controller 1 debugs the hydraulic cylinder 3 and the servo valve 2 of the six-degree-of-freedom displacement compensation platform. The six-degree-of-freedom displacement compensation platform is hinged on the upper platform 4 and the lower platform 5 by the upper platform 4 and Six hydraulic cylinders 3 between the lower platforms 5 are assembled, one hydraulic cylinder 3 is driven by one servo valve 2, and the controller 1 controls six servo valves 2, such as figure 1 shown, including the following steps:
[0056] Step A, before assembling the six-degree-of-freedom displacement compensation platform, connect the six hydraulic cylinders 3 to the oil circui...
PUM
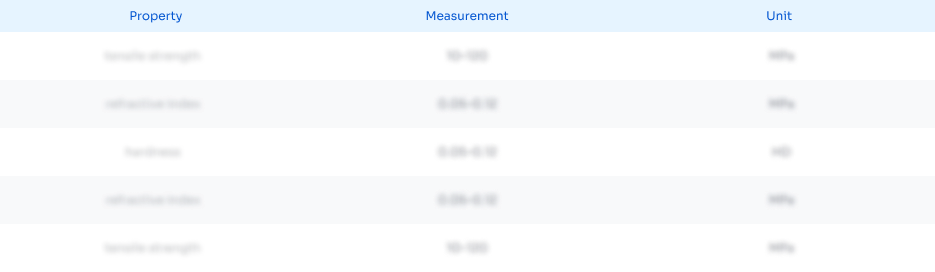
Abstract
Description
Claims
Application Information

- R&D Engineer
- R&D Manager
- IP Professional
- Industry Leading Data Capabilities
- Powerful AI technology
- Patent DNA Extraction
Browse by: Latest US Patents, China's latest patents, Technical Efficacy Thesaurus, Application Domain, Technology Topic, Popular Technical Reports.
© 2024 PatSnap. All rights reserved.Legal|Privacy policy|Modern Slavery Act Transparency Statement|Sitemap|About US| Contact US: help@patsnap.com