A butterfly grinding disc and its process for grinding the end face and annular groove of valve body parts
A technology of grinding discs and annular grooves, applied in machine tools suitable for grinding workpiece planes, wheels with flexible working parts, grinding machines, etc., can solve the problems of inability to grind, difficult for workers to operate, and reduce assembly accuracy, etc. To achieve the effect of convenient worker operation, simple grinding process and high grinding efficiency
- Summary
- Abstract
- Description
- Claims
- Application Information
AI Technical Summary
Problems solved by technology
Method used
Image
Examples
Embodiment 1
[0023] Embodiment one: if Figure 1~3 As shown, a butterfly-shaped grinding disc, which includes a rotating shaft 1, a plastic disc 2, a strip-shaped abrasive cloth 3 and a strip-shaped abrasive cloth fixing structure, the described rotating shaft 1 is fixed on the top surface of the plastic disc 2, and the described plastic disc 2 It is circular, rectangular or square. In this embodiment, the plastic disc 2 is circular. There are a plurality of grooves 4 evenly on the plastic disc 2 and along the edge of the plastic disc 2. There are arcs on the side walls of the grooves 4. shaped groove 5, the strip-shaped abrasive cloth fixing structure is arranged in the groove 4, the strip-shaped abrasive cloth fixing structure is composed of a plastic cylinder 6, a bent plate 7, a boss 8 and an arc-shaped block 9, and the arc-shaped block 9 is also It is a plastic part and is integrated with the plastic cylinder 6. The arc-shaped block 9 is arranged on the side wall of the plastic cylind...
Embodiment 2
[0032] Embodiment 2: The difference between this embodiment and Embodiment 1 is that the process of grinding the end face and the annular groove of the valve body parts with the butterfly grinding disc includes the following steps:
[0033] S1, such as Figure 4 As shown, for the tooling of the valve body 10 to be polished, the outer wall of the valve body 10 is clamped by the three-jaw chuck, and the grinding surface 11 is exposed to the outside, thereby realizing the tooling of the valve body;
[0034] S2. Rotate the three-jaw chuck at a speed of 58r / min to make the valve body 10 rotate around its own axis;
[0035] S3. Connect the rotating shaft 1 of the butterfly-shaped grinding disc to the output shaft of the grinding gun, start the grinding gun, and the grinding gun drives the plastic disc 2 to rotate at 1350r / min, and the direction of rotation is opposite to that of the three-jaw chuck;
[0036] S4. For fine grinding of the annular groove of the valve body, the plastic...
Embodiment 3
[0038] Embodiment three: the difference between this embodiment and embodiment one is that the process of grinding the end face and annular groove of the valve body parts with the butterfly grinding disc includes the following steps:
[0039] S1, such as Figure 4 As shown, for the tooling of the valve body 10 to be polished, the outer wall of the valve body 10 is clamped by the three-jaw chuck, and the grinding surface 11 is exposed outside, thereby realizing the tooling of the valve body;
[0040] S2. Rotate the three-jaw chuck at a speed of 60r / min to make the valve body 10 rotate around its own axis;
[0041] S3. Connect the rotating shaft 1 of the butterfly-shaped grinding disc to the output shaft of the grinding gun, start the grinding gun, and the grinding gun drives the plastic disc 2 to rotate at 1500r / min, and the direction of rotation is opposite to that of the three-jaw chuck;
[0042]S4. For fine grinding of the annular groove of the valve body, the plastic disk ...
PUM
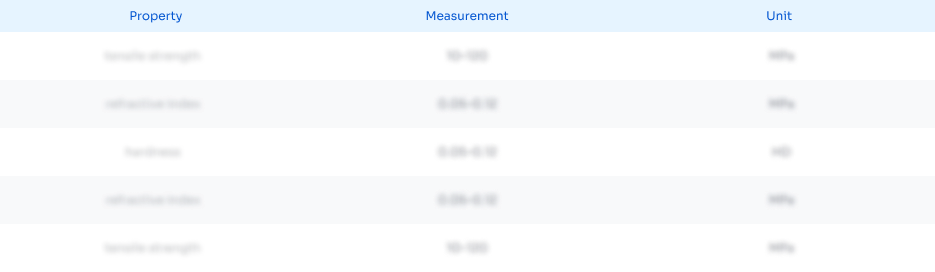
Abstract
Description
Claims
Application Information

- R&D
- Intellectual Property
- Life Sciences
- Materials
- Tech Scout
- Unparalleled Data Quality
- Higher Quality Content
- 60% Fewer Hallucinations
Browse by: Latest US Patents, China's latest patents, Technical Efficacy Thesaurus, Application Domain, Technology Topic, Popular Technical Reports.
© 2025 PatSnap. All rights reserved.Legal|Privacy policy|Modern Slavery Act Transparency Statement|Sitemap|About US| Contact US: help@patsnap.com