Automobile headlamp optical lens support structure
A technology of lens bracket and light optics, which is applied in the field of auto parts, can solve problems such as assembly difficulties, car driving danger, and headlight damage, and achieve the effect of stable bracket structure and firm fixation
- Summary
- Abstract
- Description
- Claims
- Application Information
AI Technical Summary
Problems solved by technology
Method used
Image
Examples
Embodiment Construction
[0017] refer to Figure 1-Figure 5 , a kind of automobile headlight optical lens support structure of the present invention, comprises semicircular left and right support 1,2 and at least one lens 3 that is clamped at the inner side of left and right support, as Figure 5 As shown, the left and right brackets are relatively closed to form a ring, and the inner sides of the left and right brackets are respectively provided with semicircular lens slots 5 having the same number as the lenses, and the edges of the lenses are provided with snap rings 7 , the left and right brackets are oppositely provided with two arc-shaped metal clamping shrapnels 8 on the outside of the relative closure, and the metal clamping shrapnels are buckled by the barbs 9 at both ends to the hooks respectively located on the left and right brackets. In the slot 10, the rear ends of the left and right brackets are provided with left and right bracket fixing plates 11,12. The materials of the left and rig...
PUM
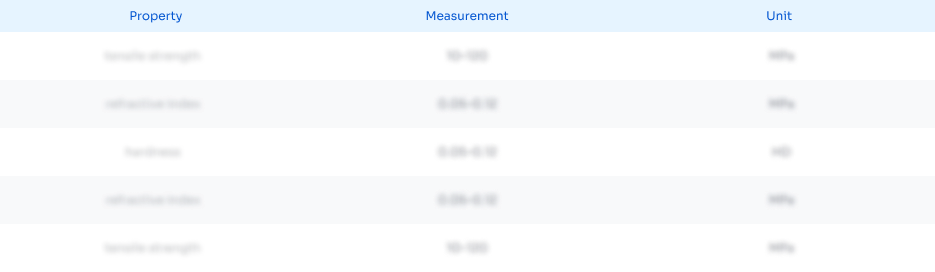
Abstract
Description
Claims
Application Information

- R&D
- Intellectual Property
- Life Sciences
- Materials
- Tech Scout
- Unparalleled Data Quality
- Higher Quality Content
- 60% Fewer Hallucinations
Browse by: Latest US Patents, China's latest patents, Technical Efficacy Thesaurus, Application Domain, Technology Topic, Popular Technical Reports.
© 2025 PatSnap. All rights reserved.Legal|Privacy policy|Modern Slavery Act Transparency Statement|Sitemap|About US| Contact US: help@patsnap.com