A testing method for real-time determination of microseismic wave velocity
A test method and technology of microseismic waves, which are applied in the measurement device, the measurement of propagation velocity, and the measurement of ultrasonic/sonic/infrasonic waves, etc., can solve the problems of unknown actual damage location, human and financial cost, seismic wave velocity error, etc., so as to solve microseismic wave The effect of possible changes in wave speed, improved accuracy, and improved positioning accuracy
- Summary
- Abstract
- Description
- Claims
- Application Information
AI Technical Summary
Problems solved by technology
Method used
Image
Examples
example 1
[0028] Example 1, such as figure 2 As shown, a microseismic monitoring system is installed in an underground project, and the microseismic monitoring system contains 16 microseismic sensors. In the existing spatial coordinate system of the microseismic monitoring system, the spatial coordinates of 16 microseismic sensors are accurately measured by the total station. The spatial coordinates of each microseismic sensor are shown in Table 1.
[0029] Table 1 Spatial coordinates of each microseismic sensor
[0030]
[0031] At 15:37:30 on July 29, 2014, an artificial blasting test was carried out in the lower lane of the 141 working face, a key area for microseismic monitoring. The location of artificial blasting is as figure 2 As shown, the spatial coordinates of the artificial blasting event accurately measured by the total station are M(4372.0, 2830.5, -73.9). The artificial blasting event is used as the microseismic source to calculate the microseismic wave velocity. ...
PUM
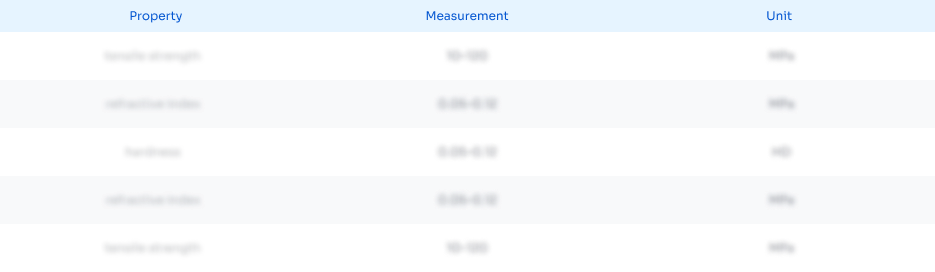
Abstract
Description
Claims
Application Information

- Generate Ideas
- Intellectual Property
- Life Sciences
- Materials
- Tech Scout
- Unparalleled Data Quality
- Higher Quality Content
- 60% Fewer Hallucinations
Browse by: Latest US Patents, China's latest patents, Technical Efficacy Thesaurus, Application Domain, Technology Topic, Popular Technical Reports.
© 2025 PatSnap. All rights reserved.Legal|Privacy policy|Modern Slavery Act Transparency Statement|Sitemap|About US| Contact US: help@patsnap.com