UAV (Unmanned Aerial Vehicle) assembling and debugging vehicle
A technology of unmanned aerial vehicles and trimming, which is applied in aircraft assembly, aircraft component testing, aircraft parts, etc. It can solve the problems of not being able to meet the production schedule, low work efficiency, and high labor intensity, and achieve shortened assembly time, convenient movement, and energy saving. Workplace Effects
- Summary
- Abstract
- Description
- Claims
- Application Information
AI Technical Summary
Problems solved by technology
Method used
Image
Examples
Embodiment Construction
[0013] An unmanned aerial vehicle assembly and debugging vehicle provided in this embodiment, such as figure 1 and figure 2 As shown, it is mainly composed of a chassis 1, a weighing pan 2, a trim device 12, a display mechanism 3, a support frame 4 and a lifting mechanism. There are four pressure sensors 5 between the weighing pan and the pressure sensor are connected to the display mechanism 3 installed on the chassis through wires. The chassis is connected to the weighing pan; T-shaped support frames 4 are respectively installed at the front and rear ends of the weighing pan, and four polyurethane rubber wheels 7 with locking mechanisms are arranged on both sides of the upper part of the support frame; A lifting mechanism is fixedly installed. The lifting mechanism is mainly composed of a motor, an electric push rod 8 and a linear guide rail 9. The electric push rod driven by the motor pushes the support rod mounted on the linear guide rail up and down. It is composed of ...
PUM
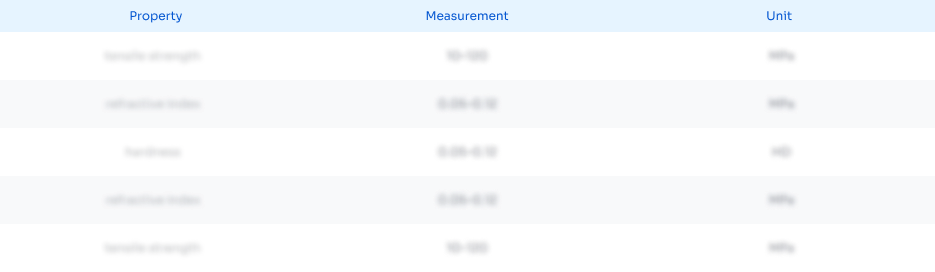
Abstract
Description
Claims
Application Information

- R&D
- Intellectual Property
- Life Sciences
- Materials
- Tech Scout
- Unparalleled Data Quality
- Higher Quality Content
- 60% Fewer Hallucinations
Browse by: Latest US Patents, China's latest patents, Technical Efficacy Thesaurus, Application Domain, Technology Topic, Popular Technical Reports.
© 2025 PatSnap. All rights reserved.Legal|Privacy policy|Modern Slavery Act Transparency Statement|Sitemap|About US| Contact US: help@patsnap.com