Pressure valve debugging system
A technology for debugging systems and pressure valves. It is used in fluid pressure actuation system testing, fluid pressure actuation devices, and mechanical equipment. It can solve problems such as affecting the cleanliness of the hydraulic system, inability to complete pressure adjustment, and insufficient wrench space. The effect of preventing the impact of cleanliness, reducing requirements, solving operating space constraints
- Summary
- Abstract
- Description
- Claims
- Application Information
AI Technical Summary
Problems solved by technology
Method used
Image
Examples
Embodiment Construction
[0022] The present invention will be described in detail below with reference to the accompanying drawings and examples.
[0023] Such as figure 1 and figure 2 As shown, the pressure valve debugging system according to the present invention includes an oil supply circuit, a pressure regulating test oil circuit and a pressure limiting oil circuit, the oil supply circuit includes at least one oil pump, and the output pipeline of the oil pump has a first output node A; The test oil circuit is connected with the first output node A, and is used for installing the pressure valve 17 to be adjusted. The pressure regulation test oil circuit includes a flow meter 14 and a pressure detection connection arranged in series between the pressure valve 17 to be adjusted and the first output node A. The input point; the pressure limiting oil circuit is connected with the first output node A, and is used to limit the pressure of the pressure regulating test oil circuit. In the present inven...
PUM
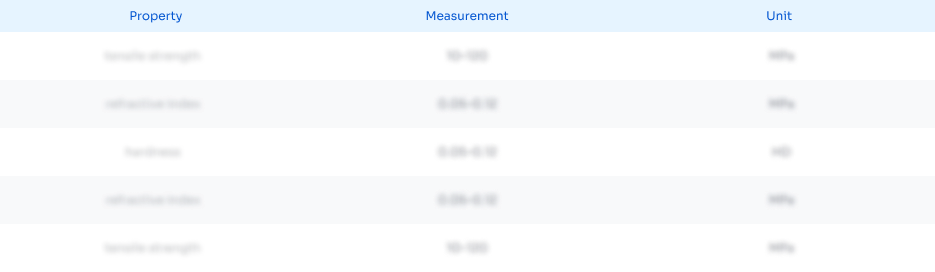
Abstract
Description
Claims
Application Information

- R&D
- Intellectual Property
- Life Sciences
- Materials
- Tech Scout
- Unparalleled Data Quality
- Higher Quality Content
- 60% Fewer Hallucinations
Browse by: Latest US Patents, China's latest patents, Technical Efficacy Thesaurus, Application Domain, Technology Topic, Popular Technical Reports.
© 2025 PatSnap. All rights reserved.Legal|Privacy policy|Modern Slavery Act Transparency Statement|Sitemap|About US| Contact US: help@patsnap.com