Reducing clamping connector for torsion detection of drive shaft
A transmission shaft and clamping technology, which is applied to measuring devices, force/torque/power measuring instruments, instruments, etc., to achieve the effect of improving work efficiency and convenient operation of variable diameter
- Summary
- Abstract
- Description
- Claims
- Application Information
AI Technical Summary
Problems solved by technology
Method used
Image
Examples
Embodiment Construction
[0019] Further illustrate the present invention below in conjunction with accompanying drawing.
[0020] Such as figure 1 As shown, the present invention includes a cylindrical jaw fixing sleeve 1 and a jaw pressing sleeve 2 threaded on the outer wall of the jaw fixing sleeve 1 . Two jacket levers 3 are arranged on the outer wall of the clamping jaw pressing sleeve 2 . The rear end of the jaw fixing sleeve 1 (that is, the installation end of the torque wrench) has a rear end cover 12, and a torque wrench connecting hole 11 is opened at the center of the rear end cover 12, and the front end of the jaw fixing sleeve 1 (that is, the clamping end) ) are connected with four circumferentially uniform clamping jaws 4 through the hinge shaft 10 .
[0021] The outer surface of the jaw 4 includes an inclined surface 4-2 that matches the front end of the jaw pressing sleeve 2, and also includes a plane 4-3 located in front of the inclined surface 4-2, through which the two outer lever...
PUM
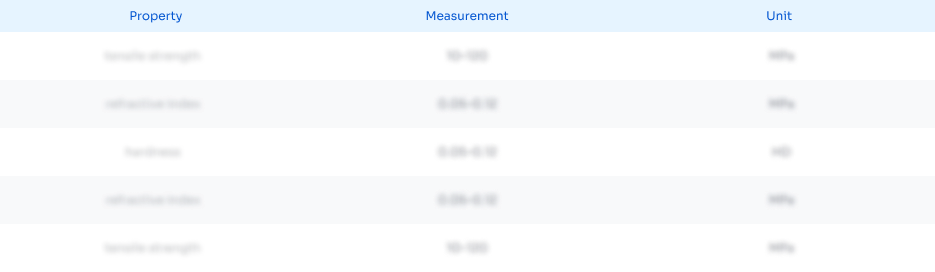
Abstract
Description
Claims
Application Information

- Generate Ideas
- Intellectual Property
- Life Sciences
- Materials
- Tech Scout
- Unparalleled Data Quality
- Higher Quality Content
- 60% Fewer Hallucinations
Browse by: Latest US Patents, China's latest patents, Technical Efficacy Thesaurus, Application Domain, Technology Topic, Popular Technical Reports.
© 2025 PatSnap. All rights reserved.Legal|Privacy policy|Modern Slavery Act Transparency Statement|Sitemap|About US| Contact US: help@patsnap.com